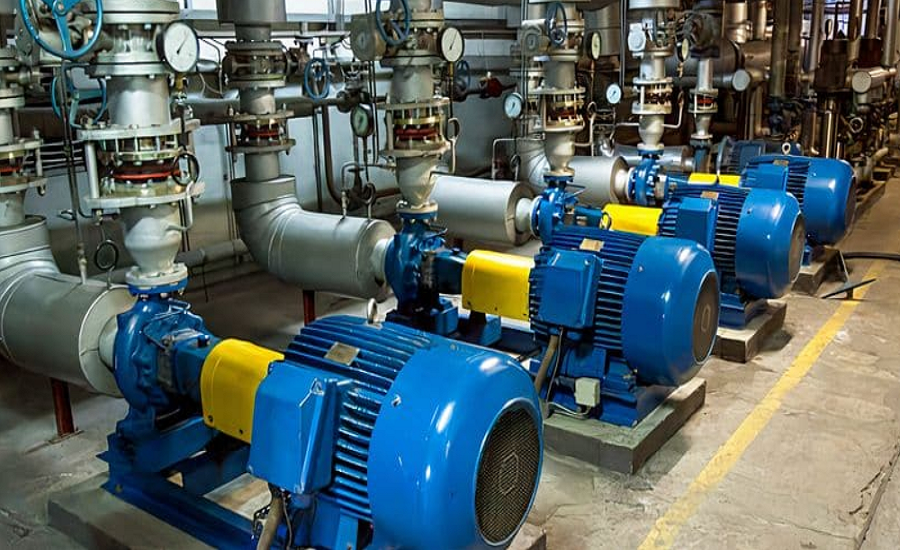
Pump systems are essential components in various industries, from water treatment and HVAC to chemical processing and oil refining. To ensure these systems operate efficiently and reliably, engineers rely on pump curves—graphical tools that represent a pump’s performance characteristics. Understanding how to read and use pump curves is crucial for selecting the right pump for a specific application and for diagnosing performance issues in existing systems.
What is a Pump Curve?
A pump curve is a graphical representation of a pump’s performance at different flow rates. It is typically provided by the pump manufacturer and shows how the head (pressure), efficiency, power consumption, and Net Positive Suction Head Required (NPSHr) change with varying flow rates.
The pump curve helps answer a fundamental question: How will this pump perform under specific system conditions?
Key Components of a Pump Curve
-
Head vs. Flow (H-Q Curve):
-
This is the most fundamental part of a pump curve.
-
The vertical axis represents the head (typically in meters or feet), which is the energy per unit weight the pump adds to the fluid.
-
The horizontal axis shows the flow rate (typically in gallons per minute, GPM, or cubic meters per hour, m³/h).
-
This curve slopes downward, indicating that as flow increases, the head produced by the pump decreases.
-
-
Efficiency Curve:
-
Overlaid on the H-Q curve, this shows how efficiently the pump operates at various flow rates.
-
Efficiency is highest near the Best Efficiency Point (BEP), which is the optimal operating point for the pump.
-
-
Power Curve:
-
Indicates the brake horsepower (BHP) or kilowatts (kW) required at different flow rates.
-
Helps in selecting the appropriate motor size and understanding energy consumption.
-
-
NPSHr Curve:
-
Shows the Net Positive Suction Head Required to avoid cavitation.
-
Ensures the system provides sufficient pressure at the pump inlet to prevent damage.
-
Why Pump Curves Matter
1. Proper Pump Selection
-
Selecting a pump without referencing its curve can lead to oversized or undersized equipment.
-
Operating too far from the BEP reduces efficiency and increases wear, energy costs, and maintenance.
2. System Design and Troubleshooting
-
Understanding how a pump interacts with a system curve (representing the frictional and static head losses in the piping system) helps engineers find the operating point—where the pump curve intersects the system curve.
-
Deviations from expected performance can indicate blockages, wear, or other system issues.
3. Energy Efficiency
-
Running a pump at or near its BEP ensures maximum energy efficiency.
-
This reduces operating costs and contributes to sustainability goals.
Real-World Example
Imagine a pump designed to deliver 100 GPM at a head of 80 feet. If the system demands a higher flow rate (say, 130 GPM), the head may drop to 65 feet, and efficiency may decline. Conversely, if the flow drops to 70 GPM, the head increases, potentially straining the pump or system. The pump curve allows operators to see these trade-offs in advance.
Conclusion
Pump curves are more than just technical graphs—they are vital tools for smart engineering decisions. By understanding how to read and apply pump curves, engineers can ensure that pump systems are efficient, cost-effective, and reliable. Whether you’re designing a new system or troubleshooting an existing one, the pump curve is your roadmap to optimal performance.