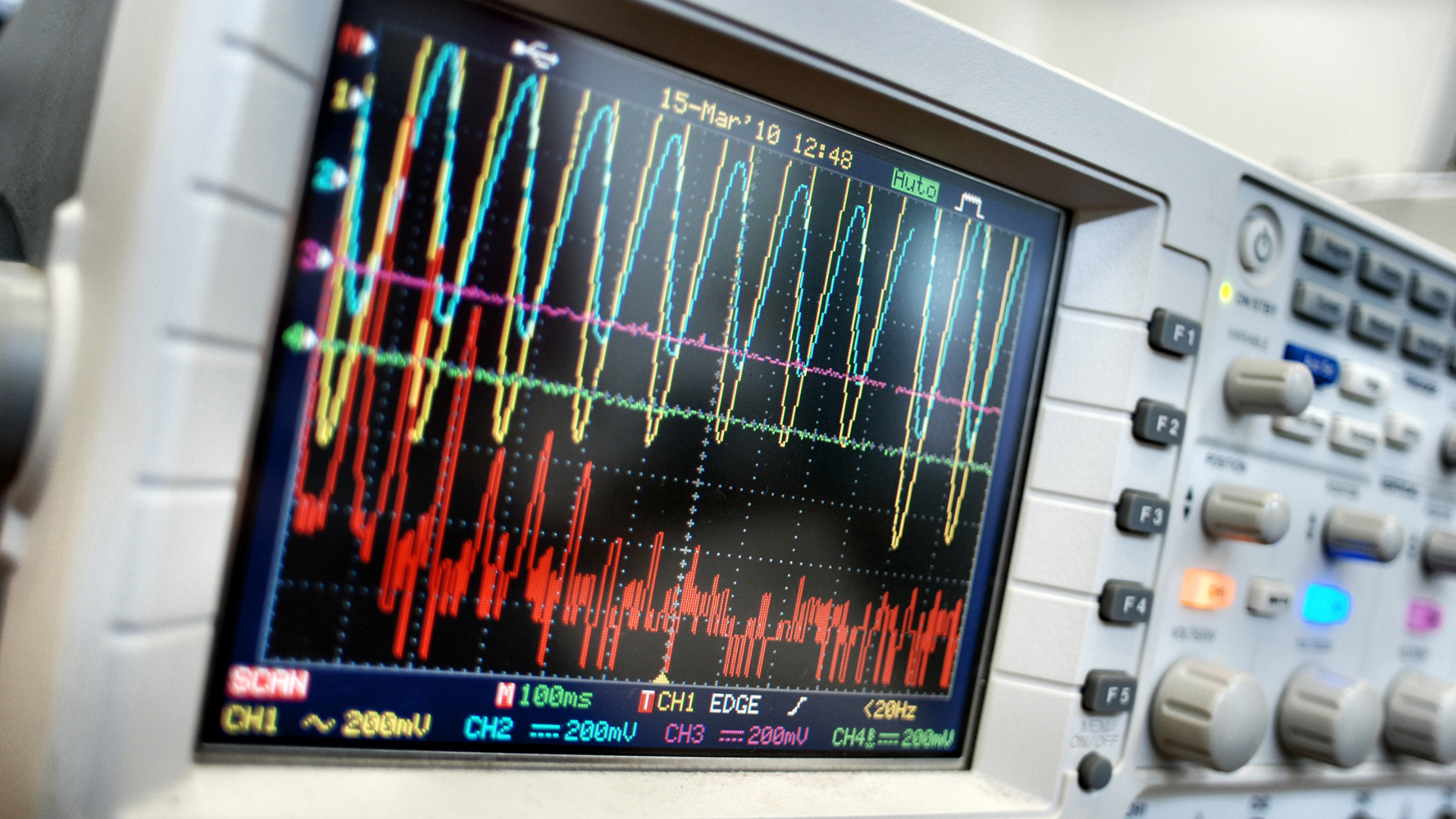
In the realm of industrial maintenance and condition monitoring vibration analysis has emerged as a cornerstone technique. It is a proactive data-driven approach that provides critical insights into the health and performance of machinery. By identifying potential issues before they lead to costly breakdowns vibration analysis services play a pivotal role in maintaining equipment efficiency and ensuring operational continuity.
This comprehensive guide explores the fundamentals of vibration analysis its benefits in condition monitoring and its role in predictive maintenance. Additionally, we’ll explain how these services improve equipment efficiency and contribute to better decision-making for industrial operations.
What Are Vibration Analysis Services?
Vibration analysis is the process of monitoring measuring and analyzing the vibration patterns of machinery and equipment. These services use advanced sensors and software to collect data on the amplitude, frequency and phase of vibrations. Deviations in these parameters often signal issues such as misalignment, imbalance, bearing wear or loose components.
By analyzing these signals technicians can pinpoint the root cause of anomalies assess the severity of potential issues and recommend corrective actions. This approach minimizes the risk of unexpected equipment failure and ensures smooth uninterrupted operations.
Benefits of Vibration Analysis in Condition Monitoring
Condition monitoring is a proactive maintenance strategy that involves tracking the health of machinery over time. Vibration analysis is a vital component of this strategy offering several key benefits:
1. Early Detection of Faults
Vibration analysis identifies potential problems at their earliest stages. Whether it’s a developing crack worn bearing or unbalanced rotor detecting these issues early prevents them from escalating into catastrophic failures.
2. Minimized Downtime
Unplanned downtime can be a significant drain on resources. Vibration analysis helps schedule maintenance activities during planned outages ensuring minimal disruption to operations.
3. Cost-Effective Maintenance
By addressing issues proactively vibration analysis reduces the need for reactive maintenance and the associated costs of emergency repairs or equipment replacements.
4. Enhanced Safety
Faulty machinery can pose serious safety risks to workers and the environment. Vibration analysis helps mitigate these risks by ensuring equipment operates within safe parameters.
5. Extended Equipment Lifespan
Regular vibration monitoring and timely interventions can significantly prolong the operational life of machinery, yielding better returns on investment.
How Vibration Analysis Services Improve Equipment Efficiency
Efficient machinery is the backbone of any industrial operation. Vibration analysis services directly contribute to improving equipment efficiency in several ways:
1. Identifying and Correcting Imbalances
Imbalances in rotating components are a common cause of energy inefficiency. Vibration analysis can detect these imbalances and guide corrective measures, ensuring smooth operation and optimal energy usage.
2. Reducing Energy Consumption
Faulty components like misaligned belts or worn bearings often lead to increased friction and energy loss. Addressing these issues through vibration analysis enhances energy efficiency and reduces operational costs.
3. Optimizing Maintenance Schedules
Rather than relying on time-based maintenance schedules vibration analysis enables condition-based maintenance. This approach ensures maintenance tasks are performed only when necessary, avoiding unnecessary disruptions and expenses.
4. Ensuring Peak Performance
By keeping machinery in peak condition vibration analysis maximizes production output and minimizes variations in product quality caused by equipment inefficiencies.
Understanding Vibration Analysis for Predictive Maintenance
Predictive maintenance is a forward-thinking approach that uses real-time data and analytics to predict when equipment will require maintenance. Vibration analysis is a critical tool for predictive maintenance offering precise insights that guide maintenance decisions.
Key Elements of Vibration Analysis for Predictive Maintenance
- Data Collection: Advanced sensors capture vibration data during machine operation providing a snapshot of its health.
- Frequency Analysis: By examining the frequency of vibrations technicians can identify the specific type of fault affecting the machinery.
- Trending and Historical Analysis: Comparing current vibration data with historical trends helps identify patterns and predict future failures.
- Root Cause Analysis: Vibration analysis pinpoints the exact cause of anomalies enabling targeted interventions.
Predictive maintenance powered by vibration analysis ensures that equipment operates reliably reducing downtime and extending the lifespan of critical assets.
The Process of Vibration Analysis Services
The process of vibration analysis typically involves several stages:
- Installation of Sensors: Sensors are strategically placed on machinery to measure vibration levels.
- Data Acquisition: Vibration data is collected while the equipment is running under normal operating conditions.
- Data Processing: Specialized software analyzes the data extracting key parameters like amplitude frequency and phase.
- Diagnostics: Technicians interpret the data to identify any deviations from normal vibration patterns.
- Recommendations: Based on the finding’s technicians provide actionable recommendations for maintenance or repairs.
Applications of Vibration Analysis Across Industries
Vibration analysis services are widely used across various industries including:
- Manufacturing: Ensuring smooth operation of conveyors, motors and production lines.
- Energy: Monitoring turbines, generators and compressors to prevent costly outages.
- Aerospace: Maintaining the reliability of critical aircraft components.
- Oil and Gas: Detecting faults in pumps, drills and pipelines to avoid environmental risks.
- Automotive: Optimizing the performance of engines and transmission systems.
Why Choose Expert Vibration Analysis Services?
While basic vibration monitoring can be performed in-house expert services bring several advantages:
- Advanced Tools and Techniques: Professional services use sophisticated equipment and techniques that provide more accurate and detailed insights.
- Skilled Technicians: Experienced analysts have the expertise to interpret complex data and offer practical solutions.
- Comprehensive Reporting: Detailed reports from experts help organizations make informed decisions about their maintenance strategies.
Conclusion
Vibration analysis services are a cornerstone of modern maintenance strategies offering unparalleled benefits in condition monitoring and predictive maintenance. By identifying potential issues early improving equipment efficiency and reducing operational costs these services ensure the reliability and longevity of critical machinery.
Whether you’re aiming to enhance operational efficiency or minimize downtime vibration analysis is an essential tool for achieving these goals. Understanding its principles and benefits empowers industries to stay ahead of potential challenges and maintain a competitive edge in their operations.
To learn more about how vibration analysis services can benefit your organization visit RMSC Colorado. Our expert team provides tailored solutions that keep your equipment running at its best.