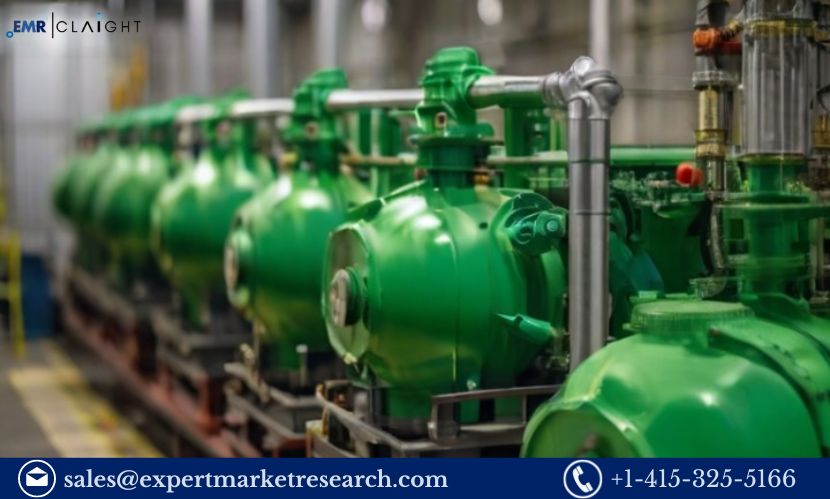
Introduction
Green hydrogen is emerging as a key player in the transition to a sustainable energy future. Unlike traditional hydrogen production methods that rely on fossil fuels, green hydrogen is produced using renewable energy sources, making it a cleaner and more environmentally friendly alternative. As the world seeks to reduce carbon emissions and combat climate change, the establishment of green hydrogen manufacturing plants represents a forward-thinking business opportunity. This Green Hydrogen Manufacturing Plant Project Report provides a detailed overview for stakeholders interested in setting up a production facility, covering market trends, infrastructure requirements, raw materials, manufacturing processes, and financial considerations.
Market Analysis
Understanding Demand
The demand for green hydrogen is driven by several factors:
- Environmental Goals: Governments and organizations worldwide are setting ambitious targets to reduce greenhouse gas emissions. Green hydrogen, produced from renewable energy sources, aligns with these sustainability goals.
- Energy Transition: As industries and transport sectors seek to decarbonize, green hydrogen offers a viable solution for sectors that are challenging to electrify, such as heavy industry and long-haul transportation.
- Technological Advancements: Innovations in electrolyzer technology and renewable energy integration are enhancing the efficiency and cost-effectiveness of green hydrogen production.
Get a Free Sample Report with Table of Contents @
Trends and Opportunities
- Government Support: Many governments are offering incentives, subsidies, and funding for green hydrogen projects as part of their climate action plans.
- Growing Investment: Investment in green hydrogen technology is increasing, driven by both public and private sectors. This trend is expected to continue as technology advances and production scales up.
- Integration with Renewable Energy: Combining green hydrogen production with renewable energy sources like wind and solar can optimize energy use and provide a stable supply of clean hydrogen.
Competitive Landscape
The green hydrogen market is competitive, with several key players and emerging entrants. Success in this market requires a focus on technological innovation, cost reduction, and strategic partnerships. Understanding competitors’ approaches and market positioning can help identify opportunities and refine your business strategy.
Plant Location and Infrastructure
Choosing the Right Location
Selecting an optimal location for a green hydrogen manufacturing plant involves several considerations:
- Proximity to Renewable Energy Sources: The plant should be located near renewable energy sources, such as wind farms or solar power plants, to ensure a steady supply of electricity for hydrogen production.
- Accessibility: The location should be well-connected to transportation networks for efficient distribution of hydrogen and raw materials.
- Regulatory Environment: Ensure the location complies with local regulations related to energy production, environmental standards, and safety requirements.
Infrastructure Requirements
-
Production Facility: The plant should be equipped with the necessary machinery and infrastructure for green hydrogen production. Key components include:
- Electrolyzers: Devices that use electricity to split water into hydrogen and oxygen.
- Renewable Energy Integration Systems: Systems to connect and manage the flow of renewable energy into the electrolyzers.
- Storage Tanks: For storing produced hydrogen safely and efficiently.
- Compression and Distribution Systems: For compressing hydrogen to required pressures and distributing it to end-users.
- Control Systems: Advanced control systems are needed for monitoring and managing the production process, ensuring safety, efficiency, and reliability.
Raw Materials and Suppliers
Key Raw Materials
- Water: The primary feedstock for hydrogen production. High-purity water is required to prevent impurities from affecting the electrolyzer.
- Electricity: Supplied from renewable sources such as wind, solar, or hydro power.
- Materials for Electrolyzers: Includes components like membranes, catalysts, and electrodes.
Supplier Relationships
Building strong relationships with reliable suppliers is crucial for ensuring a consistent supply of high-quality raw materials. Establish contracts with multiple suppliers to mitigate risks related to supply chain disruptions and price fluctuations.
Manufacturing Process
The production of green hydrogen involves several key steps:
- Energy Generation: Renewable energy sources (e.g., solar, wind) generate electricity to power the hydrogen production process.
- Electrolysis: Electricity from renewable sources is used in electrolyzers to split water into hydrogen and oxygen. The electrolysis process involves:
- Water Input: High-purity water is fed into the electrolyzer.
- Electrolyzer Operation: The electrolyzer uses electricity to separate water into hydrogen and oxygen gases.
- Hydrogen Collection: Hydrogen gas is collected and purified.
- Compression and Storage: The hydrogen gas is compressed to high pressures and stored in tanks for later use. Storage systems ensure that hydrogen remains stable and accessible.
- Distribution: Compressed hydrogen is distributed to end-users, including industries, transportation companies, and energy providers.
- Quality Control: Regular quality checks ensure that the produced hydrogen meets industry standards and specifications.
Financial Projections
Initial Investment
Setting up a green hydrogen manufacturing plant involves a significant initial investment. Key costs include:
- Electrolyzer Equipment: Expenses for purchasing and installing electrolyzers.
- Renewable Energy Infrastructure: Costs associated with integrating renewable energy sources into the production process.
- Facility Construction: Costs for building or leasing a production facility and installing necessary infrastructure.
- Storage and Distribution Systems: Expenses for storage tanks, compression equipment, and distribution networks.
Operational Costs
Regular operational expenses include:
- Electricity: Ongoing costs for purchasing or generating renewable electricity.
- Water: Costs for procuring and treating water used in the electrolyzers.
- Labor: Wages for production staff, engineers, and administrative employees.
- Maintenance: Costs for maintaining and repairing equipment and infrastructure.
Revenue Projections
Revenue will depend on factors such as production capacity, market demand, and pricing strategy. Conduct a detailed market analysis to set competitive pricing and estimate potential revenue based on expected sales volumes and customer segments.
Profit Margins
Analyzing profit margins involves considering production costs, raw material expenses, and market prices. Efficient production processes and cost management are crucial for achieving profitable margins.
Risk Management
Identifying Risks
- Raw Material Costs: Fluctuations in the prices of water and electricity can impact production costs. Establish contracts with suppliers to manage this risk.
- Technological Challenges: Rapid advancements in technology can affect competitiveness. Stay updated on technological developments and invest in innovation.
- Regulatory Changes: Changes in regulations or incentives related to renewable energy and hydrogen production can impact business operations. Monitor regulatory developments and adapt accordingly.
Mitigation Strategies
- Diversify Suppliers: Work with multiple suppliers to reduce dependency on a single source and mitigate supply chain risks.
- Invest in R&D: Allocate resources for research and development to stay at the forefront of technological advancements and improve production efficiency.
- Monitor Market Trends: Stay informed about industry trends and regulatory changes to adapt your business strategy and maintain competitiveness.
FAQ
What is green hydrogen and why is it important?
Green hydrogen is hydrogen produced using renewable energy sources to split water into hydrogen and oxygen. It is important because it provides a clean and sustainable alternative to hydrogen produced from fossil fuels, contributing to reduced greenhouse gas emissions and supporting the transition to a low-carbon economy.
What are the main steps in the green hydrogen manufacturing process?
The main steps include energy generation from renewable sources, electrolysis to split water into hydrogen and oxygen, compression and storage of hydrogen, and distribution to end-users.
How much initial investment is required to set up a green hydrogen manufacturing plant?
Initial investment varies based on plant size and location but typically includes costs for electrolyzer equipment, renewable energy infrastructure, facility construction, and storage and distribution systems.
What factors should be considered when choosing a location for the plant?
Consider proximity to renewable energy sources, accessibility for distribution, and compliance with local regulations related to energy production, environmental standards, and safety requirements.
How can I ensure the quality of green hydrogen products?
Implement rigorous quality control measures throughout the production process, including regular testing of hydrogen purity and ensuring compliance with industry standards. Maintain controlled production conditions and invest in reliable technology.
What are the major risks in green hydrogen manufacturing and how can they be managed?
Major risks include fluctuations in raw material costs, technological challenges, and regulatory changes. Manage these risks by diversifying suppliers, investing in research and development, and staying informed about market and regulatory trends.
Media Contact:
Company Name: Claight Corporation
Contact Person: Lewis Fernandas, Corporate Sales Specialist — U.S.A.
Email: [email protected]
Toll Free Number: +1–415–325–5166 | +44–702–402–5790
Address: 30 North Gould Street, Sheridan, WY 82801, USA
Website: www.expertmarketresearch.com
Aus Site: https://www.expertmarketresearch.com.au/