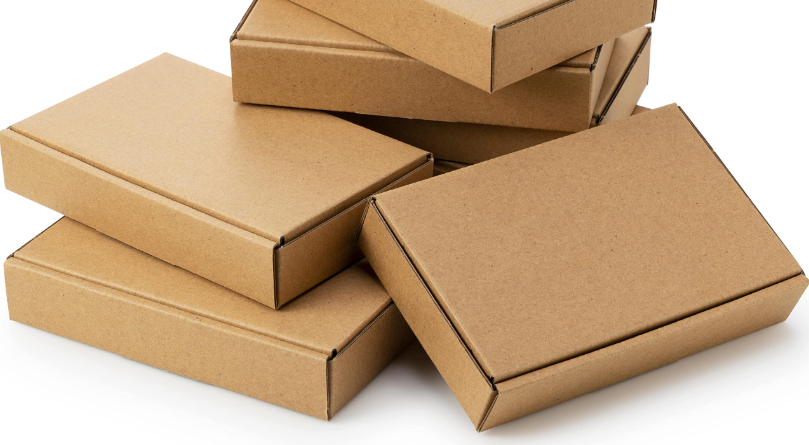
Box manufacturers play an essential role in the global economy, serving as the backbone of industries that rely on efficient packaging and transportation. Boxes, in various shapes and sizes, are used in countless applications, from shipping goods across the globe to retail packaging and even personal storage. Without box manufacturers in California, the logistics of delivering products would be far more complicated and inefficient. But what exactly does a box manufacturer do, and why are their contributions so critical?
The Evolution of Box Manufacturing
The history of box manufacturing dates back to the late 19th century, when the first corrugated cardboard box was invented in England. The initial purpose of this innovative packaging was to protect fragile goods like glass bottles and ceramics. By the early 1900s, corrugated cardboard had become the preferred method for shipping and storing products. With advancements in manufacturing techniques and the development of new materials, box manufacturing has grown to meet the needs of an increasingly global and complex market.
Box manufacturers today produce a wide variety of boxes, including those made from corrugated cardboard, paperboard, and other composite materials. These boxes come in multiple configurations, including regular slotted containers (RSC), full overlap containers (FOL), and die-cut boxes, among others. Each type of box serves a unique purpose, depending on the product’s needs, transportation method, and environmental factors.
Types of Boxes Manufactured
-
Corrugated Boxes: These are the most common type of shipping boxes and are made from a combination of fluted paper and linerboards. The flutes provide extra strength and cushioning, making corrugated boxes ideal for protecting fragile or heavy items. Manufacturers can customize these boxes in terms of strength, size, and design to meet the specific needs of their customers.
-
Paperboard Boxes: Made from a thinner form of paperboard, these boxes are typically used for retail packaging, such as cereal boxes, shoe boxes, and product packaging. Paperboard boxes are lightweight and can be printed with high-quality graphics, making them ideal for consumer-facing applications.
-
Die-Cut Boxes: These boxes are precisely cut into custom shapes to fit specific products. Die-cutting allows manufacturers to produce boxes with unique designs or unusual sizes, providing a perfect fit for delicate or oddly shaped items.
-
Specialty Boxes: Manufacturers also create specialty boxes designed for unique requirements, such as eco-friendly packaging, tamper-proof boxes, or boxes made from recycled materials. These boxes cater to the growing demand for sustainable packaging solutions.
The Manufacturing Process
The process of manufacturing boxes varies depending on the materials and types of boxes being produced. However, there are several common steps in the general production process:
-
Design and Prototyping: Box manufacturers often begin by working with clients to understand their specific needs. This may involve designing custom boxes with unique dimensions, structural strength, or aesthetic qualities. Prototypes are created and tested for durability, fit, and overall functionality.
-
Paperboard or Corrugated Material Production: For corrugated boxes, large sheets of paper are first turned into a fluted material by passing them through a series of rollers. Paperboard boxes are made from single-ply sheets that are cut and shaped into boxes.
-
Cutting and Shaping: Once the materials are prepared, the sheets are cut into the desired shapes using specialized cutting machines. For die-cut boxes, manufacturers use precision tools to cut the material into the desired shape.
-
Printing and Branding: Many boxes require branding or marketing materials, such as logos, product information, and promotional content. Manufacturers use printing technologies such as flexographic or digital printing to apply these designs onto the boxes. This step is particularly important for retail packaging.
-
Assembly and Gluing: After cutting and printing, the boxes are folded, glued, or taped into their final form. Automated machines handle much of the assembly process, ensuring uniformity and speed.
-
Quality Control: The final step is a rigorous quality control process to ensure the boxes meet the required standards for strength, durability, and appearance. Boxes are tested for things like compression strength, moisture resistance, and flexibility, depending on their intended use.
Why Box Manufacturers Matter
-
Support for E-Commerce: With the rapid rise of e-commerce, the demand for packaging solutions has skyrocketed. Box manufacturers are crucial in ensuring that the products ordered online are securely packaged for shipping. They work closely with logistics companies to create packaging that minimizes damage during transport and reduces shipping costs.
-
Sustainability Efforts: Environmental concerns have led many box manufacturers to explore more sustainable options, such as using recycled materials, reducing waste, and developing biodegradable boxes. The push toward eco-friendly packaging is expected to continue to grow as both businesses and consumers demand more sustainable solutions.
-
Global Trade: Box manufacturers enable international trade by creating sturdy packaging that allows goods to be safely transported across vast distances. Whether by air, sea, or land, boxes protect products from damage and keep them intact during transit.
-
Retail and Consumer Goods: Packaging isn’t just about functionality – it’s also a marketing tool. Retailers rely on box manufacturers to create boxes that grab the attention of consumers and reflect brand identity. A well-designed box can influence purchasing decisions and enhance the customer experience.
-
Cost-Effectiveness: Box manufacturers help businesses reduce costs by offering cost-effective solutions for packaging. By using the right materials and manufacturing techniques, manufacturers can help businesses optimize their supply chain and shipping processes.
Conclusion
Box manufacturers are integral to the global supply chain, providing businesses with the packaging solutions they need to safely transport, store, and sell products. Their role goes far beyond merely creating boxes; they are key players in supporting e-commerce, promoting sustainability, and facilitating global trade. As industries continue to evolve, the demand for innovative packaging solutions will only increase, and box manufacturers will remain at the heart of it all, ensuring products are delivered to customers in the best possible condition.