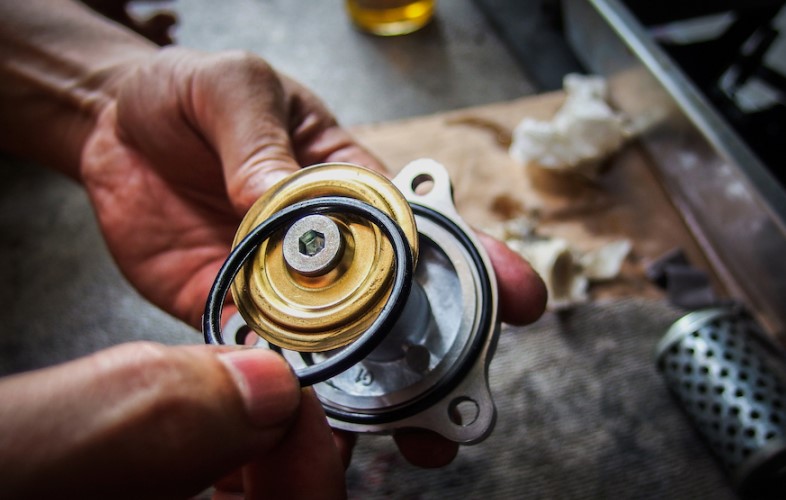
In the vast universe of mechanical components, there’s one tiny hero that rarely gets the spotlight but plays a starring role in keeping systems running smoothly the O-ring. This unassuming circular seal might look simple, but it’s a marvel of engineering that prevents catastrophic leaks, maintains pressure, and ensures machinery stays functional across industries.
What Is an O-Ring?
An O-ring is a torus-shaped (doughnut-shaped) loop typically made from elastomeric materials like rubber, silicone, or fluorocarbon. It’s designed to sit in a groove and compress between two surfaces to create a reliable seal. When pressure is applied, the O-ring deforms slightly to block any potential pathway for fluids or gases to escape.
Why O-Rings Matter
Think of O-rings as the silent guardians of countless machines and devices. They’re found in everything from car engines and hydraulic pumps to space shuttles and scuba gear. A single failure in one of these rings can mean leaks, system shutdowns, or worse—complete equipment failure.
Their importance lies in:
-
Sealing Efficiency: Prevents gas or fluid leaks under extreme pressure or temperature.
-
Cost-Effectiveness: Inexpensive to produce yet capable of saving millions in maintenance.
-
Versatility: Works across a wide range of industries, including aerospace, automotive, medical, and food processing.
-
Durability: Resistant to wear, chemicals, and temperature extremes (depending on material).
Choosing the Right O-Ring
Not all O-rings are created equal. Their effectiveness depends on selecting the right material and size for the job:
-
Nitrile (Buna-N): Great for oil and fuel systems.
-
Viton (FKM): Ideal for high temperature and chemical resistance.
-
Silicone: Perfect for medical and food-grade applications.
-
EPDM: Excellent for weather, ozone, and water resistance.
Engineers must also consider durometer (hardness), temperature range, and compatibility with the sealed medium.
Common Causes of O-Ring Failure
Despite their resilience, O-rings can fail due to:
-
Improper installation: Twisting, stretching, or nicking during assembly.
-
Chemical incompatibility: Exposure to incompatible fluids can degrade the material.
-
Temperature extremes: Excessive heat or cold can cause hardening or cracking.
-
Incorrect sizing: A poor fit can lead to extrusion or leak paths.
Regular inspection and proper maintenance are key to preventing these issues.
Small but Mighty
O-rings may be small, but their role is anything but. They are the unsung heroes that keep engines humming, airplanes flying, and pipelines sealed. Whether you’re an engineer, technician, or DIY enthusiast, understanding and respecting the power of the O-ring can save time, money, and a lot of mess.
So next time you see that little rubber loop, give it a nod of appreciation. It’s holding more together than you think.