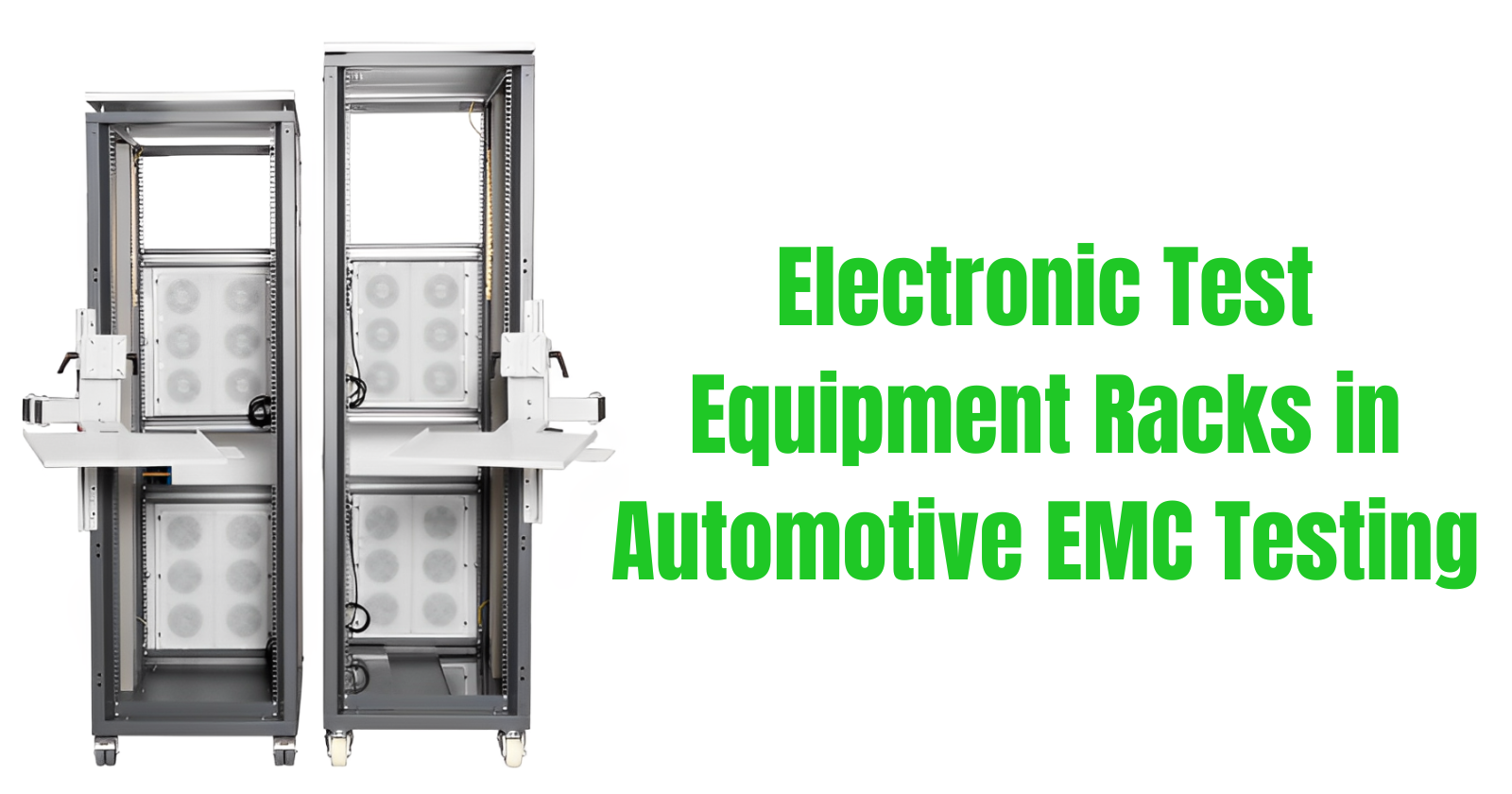
As vehicles become more connected, autonomous, and electric, the importance of electromagnetic compatibility (EMC) testing has never been greater. From infotainment systems and advanced driver-assistance systems (ADAS) to EV powertrains and wireless modules, every electronic component in a car must perform flawlessly without generating or falling victim to electromagnetic interference (EMI). This is where automotive EMC testing labs come into play—and at the heart of these labs are electronic test equipment racks.
Though they may not get the spotlight, electronic test equipment racks are the structural and organizational foundation of any high-functioning EMC lab. They support, organize, and power the sophisticated instruments that perform the measurements and analysis needed to meet industry compliance standards. Without them, labs would be cluttered, inefficient, and vulnerable to safety and reliability issues.
In this blog, we’ll dive into why these racks are essential for modern automotive EMC testing, the features that make them effective, and how companies like Orbis Systems are helping shape the future of test infrastructure.
The Growing Demands of Automotive EMC Testing
Automotive EMC testing ensures that electronic components and systems do not emit excessive electromagnetic noise and are immune to external interference. As vehicles integrate more wireless technologies—such as V2X, GPS, Bluetooth, Wi-Fi, radar, and 5G—the challenge becomes even more complex.
Testing environments must now simulate a wide range of real-world scenarios while maintaining tight control over measurement accuracy. This requires a wide array of instruments including signal generators, spectrum analyzers, EMI receivers, power supplies, RF filters, amplifiers, and shielding devices—all of which need to be arranged, powered, cooled, and interconnected efficiently.
This is where electronic test equipment racks become critical. They provide the structure, organization, and thermal management required to keep testing operations running smoothly and safely, even under high power loads and continuous use.
What Makes a Test Rack “Automotive-Ready”?
Not all racks are created equal. In automotive EMC testing environments, the racks must meet specific performance and safety requirements. Here are some of the features that define high-quality electronic test equipment racks for automotive use:
1. Modularity and Flexibility
Automotive testing setups are constantly evolving to accommodate new standards, devices, and technologies. Modular racks allow engineers to swap in and out equipment easily, reducing downtime and boosting overall lab efficiency. They also support scalable configurations—critical for multi-device and multi-standard testing.
2. Thermal Management
RF and EMC testing gear can generate significant heat, especially under high-power load conditions. Proper airflow, ventilation systems, and rack-mounted fans or heat exchangers are essential for maintaining optimal operating temperatures and preventing damage to sensitive components.
3. EMI Shielding and Grounding
Since EMC labs are particularly sensitive to electromagnetic interference, the racks themselves must contribute to reducing unwanted emissions and crosstalk. Features such as metal enclosures, shielded doors, and grounding bars help maintain electromagnetic cleanliness inside the lab.
4. Cable Management
Automotive EMC tests often require dozens of signal paths and power lines. A well-designed rack provides built-in cable trays, routing paths, and access points that prevent tangling, reduce strain on connectors, and maintain signal integrity.
5. Safety and Compliance
Safety is a top priority, especially when working with high-voltage EV components. Racks used in automotive labs must meet strict safety standards, including grounding integrity, overcurrent protection, and fire-resistant materials.
Streamlining Lab Efficiency
A chaotic test environment not only slows down testing but also increases the risk of human error. Organized electronic test equipment racks promote:
-
Faster Test Setup: With dedicated spaces for each instrument and labeled cabling, engineers can deploy and reconfigure setups with minimal effort.
-
Improved Troubleshooting: When issues arise, having a clean and logical layout makes it easier to identify faulty connections or malfunctioning equipment.
-
Higher Throughput: Automated switching systems integrated within the racks can streamline repeated testing processes, especially in production environments.
By centralizing power management, signal distribution, and cooling in one structured framework, racks become more than just equipment holders—they evolve into test system enablers.
Orbis Systems: Engineering Smart Test Infrastructure
Few companies understand the intersection of smart design and RF testing like Orbis Systems. Specializing in turnkey test solutions for telecom, electronics, and automotive sectors, Orbis integrates electronic test equipment racks into its offerings not as an afterthought, but as a core enabler of performance and scalability.
Their customized rack solutions are tailored for high-demand EMC labs, providing the necessary flexibility, shielding, and automation options needed for today’s test environments. Whether it’s a mobile rack for anechoic chambers or a full-scale multi-bay configuration for end-of-line testing, Orbis delivers with precision engineering and system-level thinking.
What sets Orbis apart is its ability to integrate measurement equipment, RF shielding, environmental control, and software control into a unified, rack-based solution. For automotive EMC labs, this means reduced time-to-test, improved measurement accuracy, and long-term reliability.
Real-World Use Case: EMC Testing in Electric Vehicles
Consider the case of electric vehicles (EVs), where high-voltage power electronics coexist with sensitive sensors, infotainment systems, and communication modules. Testing each of these components for emissions and immunity requires robust infrastructure capable of handling:
-
Multiple DUTs simultaneously
-
High-frequency and high-power measurements
-
Isolation between signal paths
-
Rapid switching between tests
-
Logging and traceability of test data
A well-constructed test rack addresses all of these needs. With integrated RF shielding, power routing, and signal switching, a single rack can support an entire test sequence—saving floor space and simplifying the testing workflow.
Preparing for the Future of Automotive Testing
As autonomous vehicles and V2X communications become mainstream, the volume and complexity of EMC tests will grow dramatically. Laboratories must be prepared with flexible infrastructure that adapts to:
-
New Frequency Bands: Especially for 5G, radar, and UWB technologies.
-
More Devices Under Test: Including ECUs, antennas, infotainment, and battery systems.
-
Faster Development Cycles: Demanding more automated, scalable test solutions.
Electronic test equipment racks will be at the center of this evolution, enabling labs to scale up without reconfiguring their entire layout each time a new device or standard comes into play.
Conclusion
While they may seem like basic infrastructure, electronic test equipment racks are essential for the smooth operation of any automotive EMC testing lab. They provide the mechanical, electrical, and thermal foundation required to support increasingly complex testing demands in today’s automotive industry.
With the right rack systems in place, engineers can reduce setup time, increase measurement accuracy, and ensure lab safety—all while keeping up with rapid innovation in connected and electric vehicles.
By partnering with trusted providers like Orbis Systems, automotive test labs can future-proof their operations and meet even the most demanding EMC standards with confidence.