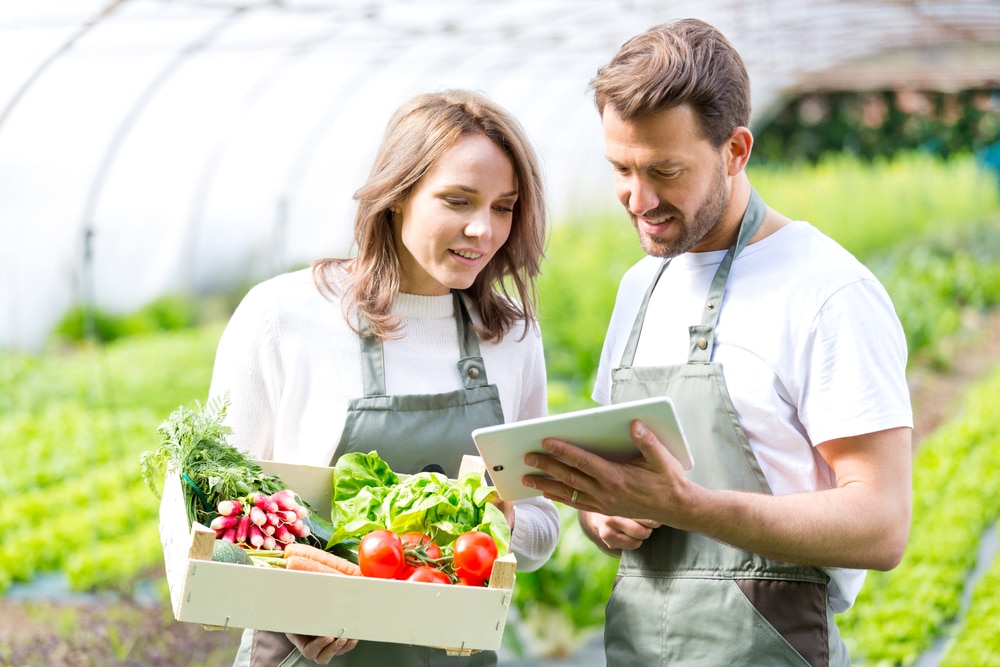
Nurseries and industrial greenhouses are under pressure to move faster, reduce waste, and meet growing demand. With multiple plant varieties, changing inventory, and short fulfillment windows, even small errors can delay shipments or cost sales.
That’s why many are turning to greenhouse inventory software.
These tools give staff real-time visibility, automate repetitive tasks, and help teams move from spreadsheets to smart systems. It’s not just about saving time—it’s about keeping orders accurate, avoiding shortages, and meeting customer expectations without burnout.
Here’s how greenhouse inventory apps help nursery and greenhouse teams simplify workflows, boost customer satisfaction, and scale up fulfillment.
Making Nursery and Greenhouse Workflows Smoother
- Live Plant Inventory Updates
In a nursery or greenhouse, plants move constantly—from propagation trays to greenhouse benches to staging areas and shipping docks. Without clear tracking, it’s easy to lose visibility.
Greenhouse inventory software solves this by showing live plant counts, locations, and readiness. Staff no longer need to walk the aisles with a clipboard to double-check availability. Barcode scanning updates inventory as plants are transplanted, pulled for shipping, or scrapped. This helps:
- Eliminate manual errors
- Save labor hours
- Ensure sales and growing teams are always aligned
For example, if a variety is being packed for shipment, the app automatically deducts it from available stock. No guesswork. No overselling.
- Easier Order Management
Orders come in fast—especially during peak seasons. Managing them manually leads to bottlenecks.
Greenhouse inventory apps allow staff to:
- Process multiple orders in batches
- Automatically generate shipping labels and invoices
- Adjust shipments if a variety runs short
- Prioritize urgent orders for key customers
This level of automation helps teams keep up with demand and reduces mistakes. It also means staff spend less time re-entering information across systems.
- Integrated Production Planning
Good inventory systems don’t just track what’s ready—they also help teams see what’s coming.
By linking inventory with growing schedules, nurseries and greenhouses can:
- Flag potential shortages before they affect orders
- Adjust planting based on upcoming demand
- Avoid overproduction of low-selling items
When a production delay pops up, the system flags it early. That gives the team time to adjust orders or schedule an extra planting cycle—without last-minute scrambling.
Better Experience for Customers
- Accurate, Real-Time Availability
Nothing frustrates customers more than placing an order and hearing, “Sorry, we’re out.” Overselling happens when inventory isn’t updated fast enough.
With greenhouse inventory apps, customers only see what’s truly available—whether it’s on an e-commerce site, a sales sheet, or a call with the team. When availability is accurate:
- Cancellations drop
- Trust increases
- Customers return
- Custom Order Fulfillment Options
Not all customers order the same way. Some want full trays. Others want mixed pallets or specific substitutions. Retailers may have different expectations than wholesalers.
Inventory apps let staff:
- Create custom availability templates
- Save preferences for high-volume buyers
- Tailor fulfillment based on customer type
This makes it easier to meet unique needs without starting from scratch for every order.
- Proactive Customer Updates
Things don’t always go to plan. Maybe weather slows a crop. Maybe a variety doesn’t finish on time.
Greenhouse inventory software can send automated alerts to customers when:
- An item ships
- A delay is expected
- A substitution is made
- An order is ready for pickup
This kind of communication builds confidence. Customers don’t have to chase updates. They stay informed automatically.
Faster, Smarter Fulfillment
- Demand Forecasting
Plant sales are seasonal, and trends shift fast. Inventory apps use past data to predict what will sell—and when. This helps growers:
- Prep the right plants in the right volume
- Order supplies ahead of time
- Avoid end-of-season waste
By reviewing sales history and seasonal cycles, teams can plan with confidence instead of relying on last year’s guesses.
- Managing Multiple Locations
Some nurseries and greenhouses operate across several sites—different greenhouses, propagation areas, outdoor fields, or warehouses.
Greenhouse inventory software tracks plants across all of them. When an order comes in, the system chooses the most efficient fulfillment location. This reduces:
- Unnecessary shipping between sites
- Order delays due to miscommunication
- Waste from pulling stock in the wrong place
Everyone sees the same data, in real time.
- Auto-Reordering Supplies
Plant production depends on inputs—pots, plugs, soil, labels, trays. Running out of any one of these can halt progress.
Inventory systems monitor supply levels. When something runs low, the system can trigger an alert or generate a purchase order. This ensures:
- Transplants don’t get delayed
- Orders aren’t held up due to missing materials
- Production runs stay on schedule
Key Features That Matter Most
For nurseries and greenhouses looking to improve operations, choose greenhouse inventory apps that offer:
- Live inventory counts and scanning tools
- Batch order processing
- E-commerce or CRM integration
- Templates for different customer types
- Production planning connections
- Multi-location support
- Automated alerts for staff and customers
- Low-supply tracking for reordering
Look for systems that are easy to train on and accessible on mobile—so staff in the field can stay connected.
Final Thoughts
Managing plant inventory in a busy nursery or greenhouse is complex. But it doesn’t have to be chaotic.
Greenhouse inventory software gives teams the tools to track, plan, and fulfill orders with fewer errors and less friction. Greenhouse inventory apps help staff focus on getting plants out the door, not chasing down paperwork or checking availability by hand.
The result? Better accuracy. Faster turnaround. Happier customers.
And a greenhouse team that runs smoother from propagation to delivery.