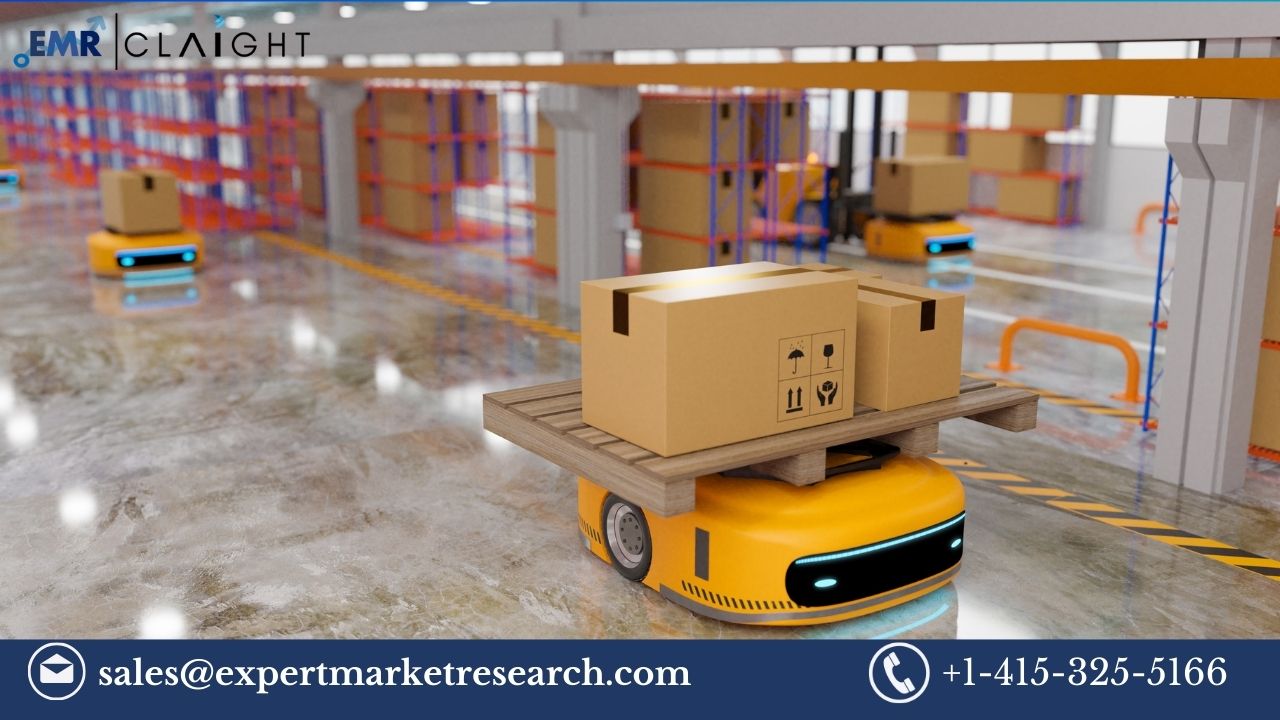
Market Outlook
The global warehouse robotics market size reached approximately USD 8.57 billion in 2024 and is projected to grow at a robust CAGR of 14.20% between 2025 and 2034, reaching nearly USD 32.33 billion by 2034. This impressive growth is driven by the rising demand for automation in warehouses, particularly in the e-commerce, retail, and industrial sectors.
As consumer expectations for faster deliveries rise, companies are turning to robotics to enhance efficiency and reduce operational costs. Automated solutions such as industrial robots, sortation systems, and mobile robots streamline warehouse processes by handling repetitive tasks with precision and speed. The growing emphasis on minimizing human error, mitigating risks, and improving workplace safety further supports the adoption of robotic systems.
The rapid expansion of e-commerce is another key driver, with warehouses under pressure to manage larger inventories while ensuring timely order fulfillment. Robotics technology is enabling warehouses to optimize space utilization, reduce turnaround times, and handle diverse product categories with ease. In addition, advancements in artificial intelligence (AI) and machine learning (ML) are enhancing robotic capabilities, making these systems more adaptive and intelligent.
Market Trends
Several notable trends are shaping the warehouse robotics market:
- Increased Adoption of Mobile Robots: Mobile robots are gaining traction due to their flexibility in navigating complex warehouse environments. These robots enhance efficiency by autonomously transporting goods and reducing the need for manual intervention. They can work around the clock, improving throughput and minimizing downtime.
- Integration of AI and Machine Learning: AI-powered robots can learn from real-time data, optimizing tasks such as picking and placing items, predicting maintenance needs, and enhancing operational efficiency. AI-driven algorithms help robots adapt to dynamic environments, enhancing decision-making and enabling predictive maintenance.
- Rise of Collaborative Robots (Cobots): Cobots work alongside human workers to handle physically demanding tasks, improving safety and productivity. They are particularly popular in e-commerce and retail warehouses, where they assist with order picking, packing, and sorting.
- Warehouse Management Systems (WMS): The integration of WMS with robotic solutions is streamlining inventory management, order processing, and real-time tracking. This integration helps warehouses achieve better visibility and control over inventory, reducing errors and improving accuracy.
- Sustainability Initiatives: Companies are increasingly adopting eco-friendly practices by using energy-efficient robots and reducing carbon emissions through optimized logistics. Robotics minimizes waste and reduces the need for excessive packaging by optimizing processes, contributing to a greener supply chain.
Market Growth
The warehouse robotics market’s growth is driven by several factors, including:
- Labor Shortages: The global labor shortage, especially in developed countries, has accelerated the adoption of robotics to maintain productivity. Warehouses are relying on robots to perform repetitive tasks, allowing human workers to focus on more complex activities.
- Cost Reduction: Robotics reduces operational costs by minimizing errors, optimizing workflows, and lowering labor expenses. Automated systems reduce reliance on manual labor, leading to long-term cost savings.
- Improved Accuracy and Speed: Robotics technology ensures precise order picking and faster processing times, enhancing customer satisfaction. Robots handle tasks with a high degree of accuracy, minimizing errors in picking and packing.
- Scalability: Robotic solutions allow warehouses to scale operations seamlessly, adapting to changing demand patterns. As order volumes fluctuate, robots provide flexibility, ensuring that warehouses can quickly ramp up or down operations.
- Technological Advancements: Innovations such as 5G connectivity, IoT, and edge computing are enhancing robotic performance, further driving market growth. These technologies improve data transfer speeds and connectivity, enabling real-time communication between robots and warehouse management systems.
Key Segments
- By Product:
- Industrial Robots: These robots perform repetitive tasks such as welding, painting, and assembling with high precision, enhancing productivity and consistency in manufacturing and logistics operations.
- Sortation Systems: Automate the sorting process, improving speed and accuracy for order fulfillment. They are essential in high-throughput environments like e-commerce fulfillment centers.
- Conveyors: Transport goods across various warehouse zones, reducing manual handling and ensuring smooth material flow.
- Palletisers: Stack goods onto pallets efficiently, optimizing space and handling heavy loads with minimal human intervention.
- Automated Storage and Retrieval Systems (AS/RS): Enable automated storage and retrieval of goods, enhancing inventory management and maximizing warehouse space.
- Mobile Robots: Navigate autonomously, transporting items between locations and reducing worker fatigue while increasing operational efficiency.
- Articulated Robots: Feature rotary joints, offering flexibility in handling complex movements, making them ideal for assembly lines and pick-and-place operations.
- Cylindrical Robots: Ideal for pick-and-place operations, leveraging cylindrical coordinates to perform precise movements.
- SCARA Robots: Perform high-speed assembly and material handling tasks with exceptional precision, commonly used in electronic manufacturing and logistics.
- Parallel Robots: Provide high-speed handling in fixed positions, often used for packaging and quality control processes.
- Cartesian Robots: Operate along linear axes, ensuring accuracy in assembly and pick-and-place operations, making them perfect for high-precision tasks.
- By Function:
- Storage: Automate the storage and retrieval of goods, optimizing space usage and ensuring accurate inventory management.
- Packaging: Streamline the packaging process by automating wrapping, labeling, and sealing, reducing processing times and human errors.
- Trans-shipment: Facilitate the movement of goods between transportation modes, ensuring smooth cross-docking operations.
- Pick & Place: Enhance accuracy and speed in picking products from shelves and placing them in designated areas, minimizing order fulfillment times.
- Palletizing & De-palletizing: Automate stacking and unstacking of products on pallets, improving efficiency and reducing worker strain.
- Transportation: Move goods across the warehouse with minimal human intervention, ensuring timely material flow.
- Others: Encompass additional functions like sorting, quality inspection, and inventory control, further optimizing warehouse operations.
- By Payload Capacity:
- Below 10 kg: Handle lightweight items, commonly used for small parts assembly and order picking.
- 11 kg to 80 kg: Ideal for medium-sized products, enhancing productivity in industries like electronics and retail.
- 81 kg to 400 kg: Manage heavy loads, reducing manual labor and streamlining workflows.
- 401 kg to 900 kg: Support large and bulky items, ensuring smooth handling in logistics and manufacturing environments.
- Above 900 kg: Handle extremely heavy goods, optimizing bulk material transport in industries like automotive and heavy machinery.
- By Component:
- Hardware: Includes robotic arms, sensors, controllers, and motors, forming the physical backbone of robotic systems.
- Software: Provides intelligence to robots, enabling automation and decision-making through algorithms and real-time data processing.
- By Application:
- Food and Beverage: Enhances efficiency in handling perishable goods, ensuring product quality and compliance with safety standards.
- Automotive: Automates parts handling and assembly processes, improving production timelines.
- Retail: Improves inventory management and order fulfillment, ensuring faster delivery times.
- Consumer Electronics: Handles delicate components with precision, reducing product damage.
- Healthcare: Ensures accuracy in handling medical supplies, enhancing patient safety.
- E-commerce: Optimizes order picking and packaging for rapid delivery, meeting growing consumer demands.
- Others: Covers industries like logistics, pharmaceuticals, and textiles, enhancing efficiency across diverse sectors.
Regional Insights
The market is witnessing notable growth across key regions:
- North America: Driven by technological advancements and the rapid expansion of e-commerce. Major players are investing heavily in automation.
- Europe: Increasing adoption due to labor shortages and high demand for efficiency in logistics and manufacturing.
- Asia-Pacific: Experiencing the fastest growth, led by China and Japan, with rising e-commerce and industrial automation demands.
- Latin America: Growing interest in automation to enhance productivity in warehouses and distribution centers.
- Middle East & Africa: Gradually adopting robotics to modernize logistics infrastructure and support economic diversification.
Key Players
- ABB Ltd.: ABB is a global leader in industrial automation and robotics. The company offers a range of robotic solutions that enhance efficiency in warehouse operations, from picking and packing to palletizing. ABB’s robots are known for their precision, reliability, and integration with advanced AI systems.
- KUKA AG: A German robotics company specializing in automation solutions, KUKA’s warehouse robots excel in material handling and logistics applications. Their robots are widely adopted for tasks like sorting, packaging, and transportation, with a focus on improving operational efficiency.
- Fanuc Corporation: Fanuc, a Japanese automation giant, is renowned for its high-performance robotic arms used in warehouses for tasks such as palletizing and order picking. The company’s robots are equipped with AI capabilities, enhancing adaptability and accuracy in complex environments.
- Yaskawa Electric Corporation: Yaskawa is a pioneer in robotic automation, offering solutions that optimize warehouse workflows. Their robots are commonly used in pick-and-place operations, packaging, and material transport, ensuring seamless integration into warehouse management systems.
- Fetch Robotics, Inc.: Specializing in autonomous mobile robots (AMRs), Fetch Robotics focuses on enhancing warehouse mobility. Their robots autonomously transport goods across warehouses, reducing human intervention and increasing productivity.
- Locus Robotics: Locus Robotics is known for its collaborative robots (cobots) designed to work alongside human workers in warehouses. These robots improve picking accuracy and speed while reducing physical strain on workers.
- IAM Robotics: IAM Robotics offers end-to-end robotic solutions for inventory management and order fulfillment. Their robots are equipped with advanced vision systems, allowing them to navigate warehouse environments autonomously and handle diverse product types.
- Honeywell Intelligrated: A subsidiary of Honeywell, Intelligrated provides comprehensive automation solutions, including robotic palletizers, sortation systems, and automated storage and retrieval systems (AS/RS). Their focus is on improving throughput and reducing operational costs.
- Swisslog Holding AG: Swisslog specializes in logistics automation, offering robotic solutions that enhance warehouse efficiency through automated picking, packing, and storage systems. The company integrates AI and data analytics to optimize workflows.
- Daifuku Co., Ltd.: Daifuku is a leading provider of material handling solutions, known for its automated storage and retrieval systems. Their robots play a crucial role in streamlining inventory management, order processing, and logistics operations.