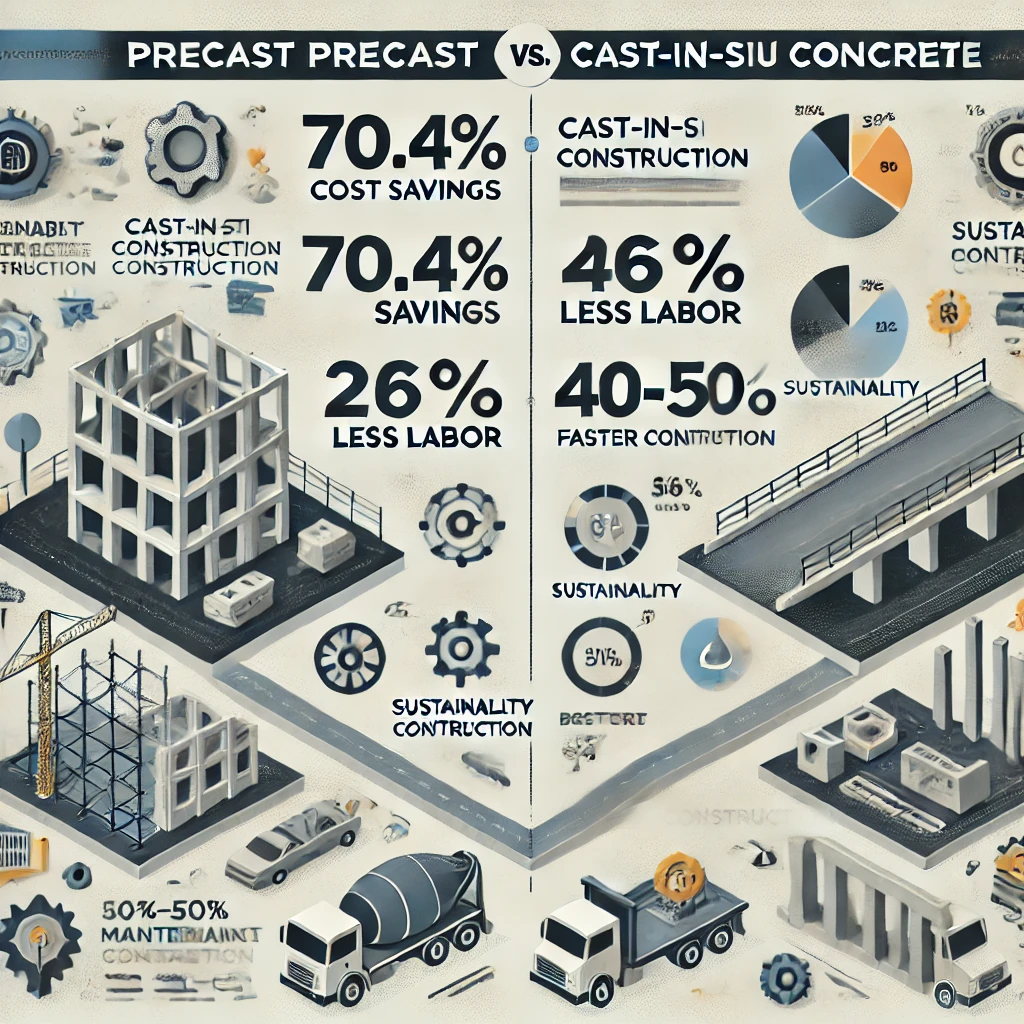
Imagine managing a large-scale construction project: every delay feels like burning money. Labor expenses pile up, materials waste away, and deadlines loom ominously. Choosing between precast and cast-in-situ concrete can make or break your budget, but what’s truly the most cost-effective option over five years? This ultimate guide reveals clear answers based on real-world data, industry insights, and compelling case studies.
Key Findings (backed by 5-year comprehensive data):
✅ 70.4% cost savings when using precast vs. cast-in-situ. ✅ Material wastage drops significantly with precast, slashing expenses. ✅ Precast requires 26% fewer workers, drastically reducing labor costs. ✅ Construction timelines shrink by 40–50% with precast. ✅ Lifecycle maintenance costs of precast are significantly lower. ✅ Precast offers superior environmental sustainability.
1. Material Efficiency: Unlocking Massive Hidden Savings
Material waste silently drains your budget. Every spill, error, or weather-damaged form adds unnecessary expenses.
Precast Advantages:
- Manufactured off-site under stringent quality control.
- Significantly less material wastage; excess materials are recycled.
Cast-In-Situ Drawbacks:
- On-site batching increases material spills and waste.
- Susceptible to weather damage, driving reworks and added costs.
Result: Precast concrete reduces material-related costs drastically, offering predictability and quality assurance.
2. Labor Costs: Less Manpower, Greater Efficiency
Labor isn’t merely about wages—it’s productivity and safety costs rolled into one.
Precast Advantages:
- Requires 26% fewer workers compared to cast-in-situ.
- Eliminates formwork labor since elements arrive ready-to-install.
- Reduces on-site risk, cutting down insurance and indirect costs.
Cast-In-Situ Drawbacks:
- Necessitates skilled labor for on-site pouring, formwork, curing.
- Higher supervisory and indirect labor costs.
Result: Choosing precast significantly lowers labor expenditure, boosting profitability.
3. Construction Time: Why Speed is Your Competitive Edge
Completing projects faster isn’t just efficient—it accelerates revenue and ROI.
Precast Advantages:
- Project timelines cut by 40–50%.
- Immediate installation upon delivery eliminates delays.
- Just-in-time (JIT) deliveries reduce scheduling complexities.
Cast-In-Situ Drawbacks:
- Longer processes: curing times, site prep, and scaffolding.
- Weather-dependent timelines frequently causing costly delays.
Case Example: A high-rise using precast finished six months early, saving millions compared to an equivalent cast-in-situ project.
4. Lifecycle & Maintenance: The Hidden Long-Term Savings
Initial construction costs are just the beginning; long-term durability defines actual savings.
Precast Advantages:
- Superior durability through controlled curing.
- Lower long-term maintenance due to fewer cracks and repairs.
Cast-In-Situ Drawbacks:
- Prone to weather-induced cracking and costly repairs.
- Ongoing maintenance quickly offsets initial cost savings.
Result: Precast concrete significantly reduces lifecycle expenses.
5. Sustainability Impact: Profit from Going Green
Environmental responsibility isn’t just ethical—it boosts profitability.
Precast Advantages:
- Lower carbon footprint through optimized manufacturing.
- High recyclability and minimal waste.
Cast-In-Situ Drawbacks:
- Higher emissions from on-site batching and frequent transportation.
- Increased waste leading to higher disposal costs.
Real-World Case Study: Concrete Data, Solid Results
A detailed analysis of a large infrastructure project over five years:
Metric | Precast Concrete | Cast-In-Situ Concrete |
---|---|---|
Total Cost Savings | ✅ 70.4% Savings | ❌ Increased Costs |
Labor Costs | ✅ 26% Lower | ❌ Higher |
Construction Timeline | ✅ 45% Faster | ❌ Prolonged Schedule |
Maintenance | ✅ Low | ❌ High |
Environmental Impact | ✅ Reduced Impact | ❌ Higher Emissions |
Conclusion: The data confirms precast’s clear dominance in cost-effectiveness, efficiency, and sustainability.
How Tekance Maximizes Precast Cost Efficiency
Adopting precast alone isn’t enough. Precise detailing makes the difference between good savings and great savings.
Tekance Detailing Services:
- Generates precise precast shop drawings to cut material wastage.
- Ensures perfect structural alignment, eliminating costly reworks.
- Optimizes schedules, enabling faster project completion and maximum ROI.
Partnering with Tekance translates into superior cost performance and exceptional quality control.
FAQs: Key Questions Answered
Q: Is precast always cheaper?
A: Initially, precast might cost more due to molds and logistics. However, long-term savings from reduced labor and faster timelines typically outweigh these initial investments.
Q: Is precast concrete more durable?
A: Yes, factory-controlled production enhances strength and durability.
Q: When might cast-in-situ be preferable?
A: For highly customized projects or intricate designs, cast-in-situ can offer greater flexibility.
Final Verdict: Why Precast Concrete is Your Winning Choice
When your goals are clear—reduce costs, accelerate timelines, and maximize sustainability—precast concrete consistently outperforms cast-in-situ methods.
With Tekance’s expertise, your precast projects aren’t just cost-effective—they’re profitable, sustainable, and industry-leading.
👉 Ready to dramatically enhance your project’s profitability and efficiency? Tekance is here to help.
Learn about Expert Rebar Detailing Services for Cost-Effective Construction