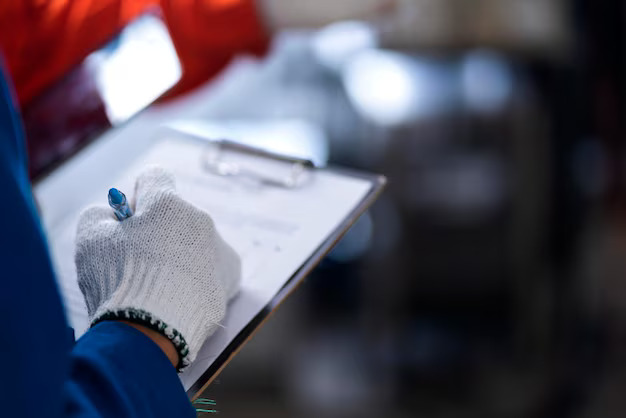
Every company’s first concern is cutting running expenses, yet many ignore the effects of a well-considered maintenance schedule. By minimizing unplanned breakdowns, prolonging the lifetime of equipment, and so cutting expenses, preventative maintenance plans can greatly help. Using proactive maintenance, companies can avoid expensive repairs, maximize resources, and raise general effectiveness. This paper investigates how a well-organized maintenance schedule might enable companies to lower expenses and raise production.
Knowing Preventive Maintenance Plans
A preventative maintenance schedule is a methodical way to keep facilities and machinery in good condition before issues start. Instead of waiting for a breakdown to happen, companies routinely check, service, and replace parts to make sure equipment stays in the best shape. These designs can be used on everything from office HVAC systems to manufacturing gear and are tailored to fit the requirements of many sectors.
The Main Advantages of Preventative Maintenance Plans
-
Frequent maintenance guarantees ongoing operations by helping to avoid unplanned equipment failures.
-
Planned maintenance helps machines to remain in the best shape, therefore postponing the need for expensive replacements.
-
Correcting little problems before they become more serious helps companies avoid costly emergency repairs.
-
Maintaining well-kept equipment lowers occupational hazards and liability concerns.
-
Well-kept machinery runs at maximum efficiency, which lowers material waste and energy usage.
Preventive Maintenance Strategies for Cost-saving
1. Schedule Routine Inspections
Routine inspections find possible issues before they become more serious. Companies should set up a disciplined inspection program to guarantee that every piece of equipment is routinely examined for wear and tear. To keep the best performance, inspections should encompass lubrication, electrical components, moving parts, and safety aspects.
2. Make Purchases of Quality Maintenance Tools and Software
Managing preventative maintenance with contemporary technologies helps to simplify processes and lower expenses. Tracking maintenance schedules, tracking equipment health, and offering data-driven insights to maximize service routines, Computerised Maintenance Management Systems (CMMS) can Additionally help to increase the accuracy and efficiency of maintenance operations is investing in sophisticated tools and diagnostic equipment.
3. Coach Staff Members on Appropriate Equipment Use
One main reason equipment breaks is employee abuse. Companies should offer thorough instructions on how to correctly run machinery, perform regular maintenance, and spot early mechanical problems. Well-trained staff members help to reduce repair expenses and breakdowns.
4. Stock Vital Spare Parts
Having basic replacement parts on hand helps to avoid protracted downtime during necessary repairs. Companies should evaluate their essential equipment and stock required replacement components to lower the possibility of supply chain problems causing delays.
5. Track Equipment Performance Indices
Monitoring performance statistics helps companies spot areas of inefficiency and project possible breakdowns. Key performance indicators (KPIs) like energy consumption, manufacturing rates, and maintenance costs can offer insightful information for improving maintenance plans and the best use of resources.
6. Work with Dependable Maintenance Service Providers
Hiring seasoned companies to handle maintenance guarantees quick repairs and excellent service. For specialized equipment maintenance, working with experts outside of your company can be less expensive than engaging inside specialists for every technical necessity.
Approaches Specific to Industries for Maintenance
-
Production Facilities and Manufacturing Sites: Preventive maintenance is especially important in factories since they depend on automated systems, conveyors, and large machinery. Component replacements, alignment checks, and regular lubrication help to prevent significant interruptions and preserve manufacturing effectiveness.
-
Logistics Centres and Warehouses: To ensure flawless operations, forklifts, conveyor belts, and storage shelves need constant maintenance. Preventive actions provide perfect inventory control by lowering equipment failures and accident rates.
-
Business Houses: Regular servicing of lifts, HVAC systems, and electrical infrastructure helps to preserve energy efficiency and save running costs. Structured maintenance programs help companies avoid costly emergency repairs.
-
Construction and heavy machinery: Extreme wear and tear goes on for excavators, cranes, and bulldozers. Including structural inspections, fluid checks, part replacements, and preventive maintenance, helps to extend their lifetime and save repair costs.
Cost Optimising with Strategic Maintenance Investments
Although first commitment is required for a preventative maintenance plan, over time the savings exceed the expenses. Companies should do a cost-benefit study to ascertain how much-planned maintenance will save versus reactive repairs financially. To maximize efficiency and cost-effectiveness, a well-organized maintenance program should fit operational goals, financial restrictions, and industry standards.
The Part Baler Service Plays in Reducing Costs
Installing baler service can help companies managing significant amounts of recyclable materials cut running costs even more. Waste products are compressed using balers, therefore facilitating disposal and recycling. Maintaining a well-kept baler helps to lower waste management costs, increase workplace safety, and support environmental initiatives. Baler regular maintenance guarantees flawless performance, therefore preventing expensive breakdowns and downtime.
Summary
Cost containment and operational effectiveness depend critically on a well-designed maintenance schedule. Following preventative maintenance schedules increases equipment lifetime, decreases repair costs, and helps to minimize downtime. Investing in regular inspections, staff training, performance monitoring, and strategic outsourcing will help companies maximize maintenance costs while preserving output. Furthermore, baler service can enable companies to effectively control waste and support general cost cutting. Giving preventative maintenance top priority guarantees any sector a competitive edge and long-term financial stability.