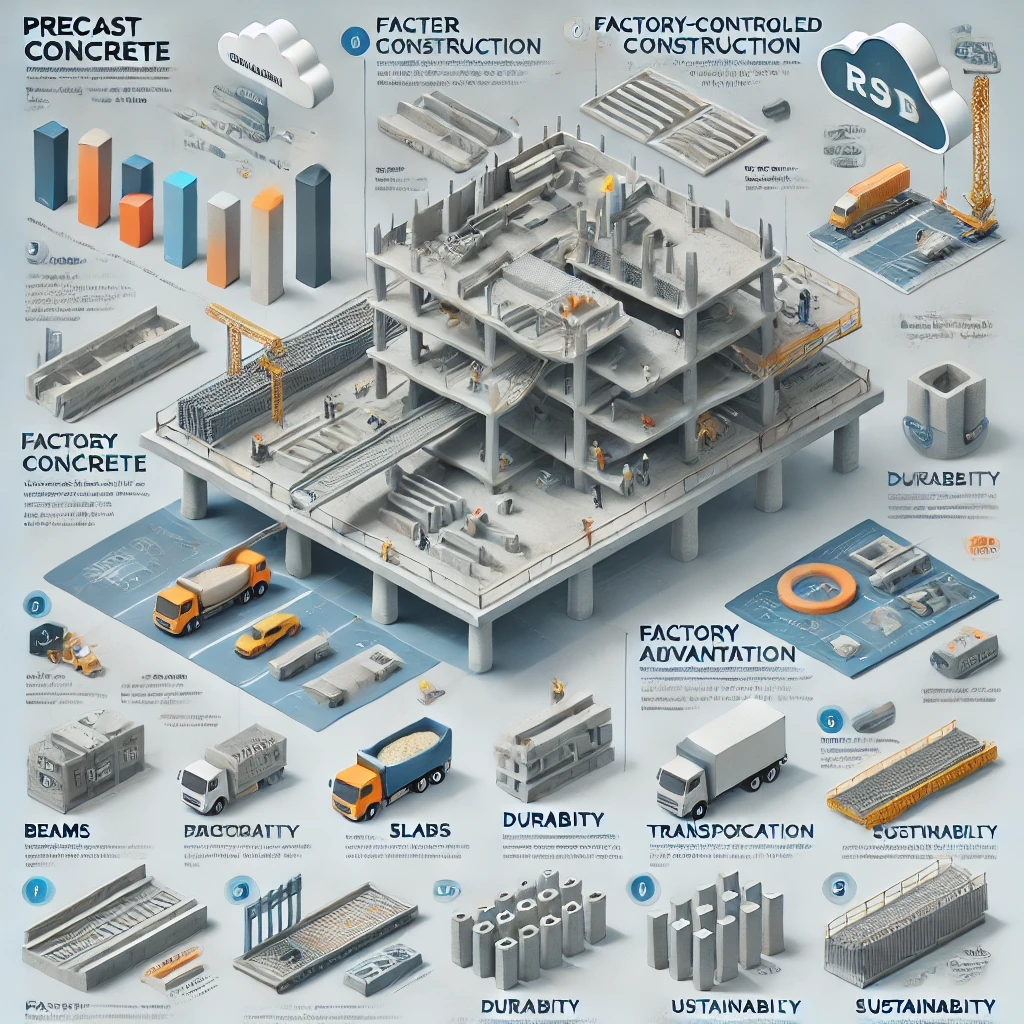
Introduction: Why Precast Concrete is Revolutionizing Construction
Precast concrete components are transforming the construction industry, making projects faster, more cost-effective, and structurally superior. Whether it’s residential buildings, bridges, highways, or industrial structures, precast concrete is reshaping the way we build.
But what exactly are precast concrete components, and why are they preferred over traditional methods?
In this in-depth guide, you’ll learn:
- What precast concrete components are
- How they compare to cast-in-place concrete
- The major advantages they offer
- The latest industry trends and innovations
Let’s dive into everything you need to know about precast concrete and why it’s a game-changer for modern construction.
What Are Precast Concrete Components?
Precast concrete components are factory-manufactured concrete elements that are later transported to a construction site and assembled. Unlike cast-in-place concrete, which is poured and cured on-site, precast concrete is produced under controlled conditions for superior quality and consistency.
Key Benefits of Factory Production
✅ Higher Quality Control – Every piece undergoes rigorous testing before delivery. ✅ Faster Construction – Components arrive ready for assembly, reducing project timelines. ✅ Greater Durability – Optimized curing conditions enhance strength and lifespan.
These advantages make precast concrete a preferred choice for developers and contractors worldwide.
Precast Concrete vs. Cast-in-Place Concrete: A Quick Comparison
Feature | Precast Concrete | Cast-in-Place Concrete |
---|---|---|
Manufacturing | Made in a factory | Poured and set on-site |
Construction Speed | Fast assembly | Time-consuming curing process |
Quality Control | High – factory-tested | Variable – depends on site conditions |
Cost Efficiency | Saves time and labor | Longer work hours, more on-site waste |
Durability | Stronger due to controlled curing | More prone to environmental conditions |
Customization | Available in various shapes, sizes, and finishes | Limited to on-site constraints |
👉 Verdict: Precast concrete is the clear winner for projects that require speed, durability, and cost savings.
Why Precast Concrete Components Are a Smart Choice
🚀 1. Faster Construction Time
Since precast components are pre-made, they only need to be transported and assembled at the site. This can cut weeks or even months off the project schedule compared to traditional construction methods.
🔥 2. Superior Strength & Durability
Precast concrete is cured under optimal factory conditions, making it stronger and more resistant to weather, fire, and wear. It lasts 50-100 years, outlasting many other building materials.
💰 3. Cost-Effective in the Long Run
While the initial cost of precast concrete might be slightly higher, it saves money through:
- Reduced labor costs
- Faster project completion
- Minimal material waste
🔍 4. Better Quality Control & Precision
Every precast component undergoes rigorous testing before leaving the factory, ensuring that only flawless, structurally sound elements reach the construction site.
🌱 5. Eco-Friendly & Sustainable
Precast concrete reduces construction waste, and many manufacturers use recycled materials in the production process, making it a greener alternative to traditional methods.
Types of Precast Concrete Components & Their Uses
🏗️ 1. Precast Beams
Function: Provide horizontal support for floors, roofs, and bridges.
Types:
- I-Beams – Common for bridges and commercial buildings.
- T-Beams – Provide additional support and load-bearing capacity.
- L-Beams – Used in modular construction.
🏢 2. Precast Slabs
Function: Used for floors and roofs.
Types:
- Hollow-core slabs – Lightweight and highly durable.
- Solid slabs – Ideal for high-rise buildings.
- Double-T slabs – Commonly used in stadiums and parking garages.
🏡 3. Precast Walls
Function: Act as load-bearing or decorative elements.
Types:
- Load-bearing walls – Used in apartment buildings and industrial structures.
- Non-load-bearing walls – Primarily decorative or used for partitions.
- Insulated panels – Enhance energy efficiency in buildings.
🏗️ 4. Precast Columns
Function: Vertical elements that support loads from beams and slabs.
Common Uses: Multi-story buildings, bridges, and warehouses.
🏠 5. Other Precast Elements
- Precast Stairs – Fast and easy installation.
- Precast Facades – Aesthetic enhancement for building exteriors.
- Precast Foundations – Stronger and more durable than traditional foundations.
How Precast Concrete Components Are Made
🏭 The Precast Production Process:
1️⃣ Mold Creation – A mold is designed to form the desired shape. 2️⃣ Concrete Pouring – High-quality concrete is poured into the mold. 3️⃣ Reinforcement – Steel bars or fiber reinforcements are added. 4️⃣ Curing – The component is cured under controlled conditions. 5️⃣ Quality Testing – Each unit undergoes strict quality control. 6️⃣ Transportation – Ready-to-install elements are shipped to the site.
This streamlined factory-based production ensures high precision, minimal defects, and superior durability.
Industry Trends & Innovations in Precast Concrete (2025 & Beyond)
🔹 3D Printing in Precast Construction – Automating complex designs and reducing material usage. 🔹 Smart Concrete with Sensors – Enhancing real-time monitoring of structural health. 🔹 Sustainable Materials – Increasing the use of recycled concrete and low-carbon cement. 🔹 Modular Precast Solutions – Rapid urban housing development with prefabricated units.
👉 Stay Ahead: Adopting these trends can increase efficiency and profitability in construction projects.
Frequently Asked Questions (FAQs)
❓ Is precast concrete stronger than traditional concrete?
Yes! Precast concrete undergoes controlled curing, making it stronger and more durable than cast-in-place concrete.
❓ How long does precast concrete last?
With proper maintenance, precast concrete structures can last 50 to 100 years.
❓ Is precast concrete cost-effective?
Although the initial cost may be higher, precast concrete reduces labor, construction time, and long-term maintenance costs, making it more cost-effective in the long run.
❓ Can precast concrete be customized?
Yes! Modern manufacturing techniques allow for customization in shape, size, and finish to fit any project’s needs.
Conclusion: Why Precast Concrete is the Future of Construction
Precast concrete is reshaping modern construction by offering unmatched speed, strength, and sustainability. With continued advancements in technology and design, the adoption of precast solutions will only grow.
Need Expert Precast Detailing Services? ✅ High-precision detailing to prevent costly site errors ✅ Faster project timelines with pre-engineered components ✅ Guaranteed quality with industry-leading standards.
Learn about Expert Rebar Detailing Services for Cost-Effective Construction