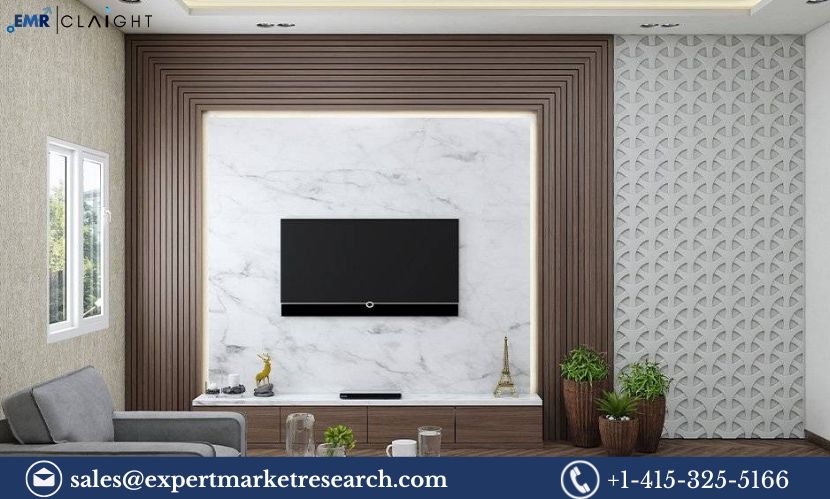
Introduction
Polyvinyl Chloride (PVC) panels have gained immense popularity as an alternative to traditional materials like wood, metal, and stone in various applications, such as construction, interior design, and furniture making. PVC panels are durable, lightweight, moisture-resistant, and easy to maintain, making them ideal for use in both residential and commercial properties. These panels are used in wall cladding, ceilings, flooring, partitions, and decorative applications, offering aesthetic appeal and functional benefits. The PVC Panel Manufacturing Plant Project Report aims to provide a detailed analysis of the feasibility, market demand, production process, raw materials, plant setup, and financial outlook for setting up a PVC panel manufacturing plant. With the increasing demand for cost-effective and sustainable building materials, this report offers crucial insights for entrepreneurs, investors, and businesses looking to enter the PVC panel production industry.
Market Overview
Growing Demand for PVC Panels
The demand for PVC panels has witnessed significant growth in recent years, driven by factors such as:
- Durability and Low Maintenance: PVC panels are highly durable, resistant to moisture, and require minimal maintenance. This makes them an attractive option for residential, commercial, and industrial applications, particularly in regions with high humidity levels or fluctuating weather conditions.
- Eco-friendly and Cost-effective: As sustainability becomes a growing concern across industries, the demand for eco-friendly building materials has risen. PVC panels offer a sustainable alternative to conventional materials like wood and metal, as they can be recycled and require less maintenance over time. Additionally, their cost-effectiveness makes them popular among budget-conscious consumers and businesses.
- Aesthetic Appeal: PVC panels are available in a wide range of designs, textures, and colors, making them an excellent choice for decorative applications. They can replicate the appearance of wood, marble, and other premium materials, offering a stylish yet affordable solution for interior design.
- Versatility in Applications: The versatility of PVC panels is another key factor driving their demand. They are used in a wide variety of applications, including wall cladding, ceilings, partitions, flooring, and even exterior facades. Their adaptability to different settings, from homes to offices and industrial spaces, makes them a popular choice across sectors.
Get a Free Sample Report with Table of Contents@
Regional Demand
- Asia-Pacific: The Asia-Pacific region is one of the largest markets for PVC panels, with countries like China, India, and Japan leading the demand. The rapid urbanization, infrastructure development, and growing construction industry in the region are key drivers of this demand. Additionally, the rising middle class in countries like India is further fueling the adoption of PVC panels in residential and commercial properties.
- North America and Europe: North America and Europe are also significant markets for PVC panels, driven by the increasing use of these materials in both residential and commercial construction. The growing trend towards sustainable construction materials and the preference for low-maintenance solutions are contributing to the rise in demand in these regions.
- Middle East and Africa: The Middle East and Africa are emerging markets for PVC panels, with the growing construction and real estate sectors providing opportunities for expansion. The demand for PVC panels in these regions is expected to rise as the construction industry continues to thrive, particularly in countries with extreme weather conditions.
Market Trends
- Sustainability and Green Building Practices: As the demand for sustainable construction materials grows, PVC panels are becoming increasingly popular due to their recyclability, energy efficiency, and long lifespan. The trend towards eco-friendly building materials, especially in the context of green building certifications, is driving the market for PVC panels.
- Customization and Design Innovations: The demand for customized PVC panels with unique designs, textures, and finishes is increasing. Manufacturers are focusing on developing high-quality, innovative products that can meet the aesthetic and functional requirements of modern interior design and construction projects.
- Growth of Modular and Prefabricated Construction: The growing adoption of modular and prefabricated construction methods is further boosting the demand for PVC panels. These materials are lightweight, easy to install, and can be used in off-site manufacturing of modular buildings and homes.
Feasibility Study
1. Capital Investment
Establishing a PVC Panel Manufacturing Plant requires significant initial investment, which includes the following key components:
- Land and Infrastructure: The cost of acquiring land and building the manufacturing plant is one of the largest components of the capital investment. The location should be chosen based on proximity to raw material suppliers, transportation networks, and target markets.
- Machinery and Equipment: The manufacturing process for PVC panels involves several steps, including extrusion, lamination, and cutting. Key machinery required for the production of PVC panels includes:
- Extruders: Used to create the PVC panels by forcing the polymer through molds.
- Laminating Machines: Used to apply decorative finishes or coatings to the panels.
- Cutting and Shaping Machines: For cutting the panels into desired sizes and shapes.
- Packaging Machines: For packaging the final product in bulk or individual packages.
- Licensing and Permits: Regulatory approvals, licenses, and certifications, including environmental and safety standards, will be required to operate a PVC panel manufacturing plant. These may include pollution control, waste management, and product quality certifications.
2. Raw Materials
The primary raw materials required for manufacturing PVC panels include:
- PVC Resin: The key ingredient in PVC panel production, PVC resin is sourced from petrochemical plants. It is available in powder or pellet form and is the base polymer used in the extrusion process.
- Additives: Additives such as plasticizers, stabilizers, and fillers are mixed with the PVC resin to enhance the material’s properties, including flexibility, durability, and fire resistance. The exact additives used depend on the desired characteristics of the final product.
- Decorative Films or Laminates: For aesthetic purposes, PVC panels are often laminated with decorative films or coatings. These films can replicate wood, marble, or other premium materials and are available in a wide range of designs and textures.
- Pigments and Dyes: To achieve the desired colors, pigments and dyes are added to the PVC resin or to the surface of the panels during the manufacturing process.
3. Production Process
The production of PVC panels involves the following main steps:
1. Compounding
The first step in the production process is to mix the PVC resin with additives such as plasticizers, stabilizers, and fillers. This mixture is known as the compound and is prepared in an extruder or compounding machine.
2. Extrusion
The prepared PVC compound is fed into an extruder, where it is melted and forced through a die to form the desired shape of the PVC panel. The extruder helps shape the compound into continuous sheets of PVC that are then cut into panels of the required size.
3. Lamination
For decorative purposes, the PVC panels are often laminated with a decorative film or coating. The panels are passed through a lamination machine, where the film is applied to the surface of the panel under heat and pressure.
4. Cooling and Cutting
After extrusion and lamination, the panels are cooled and then cut into the desired size and shape. Cutting machines ensure precise dimensions for the finished product.
5. Quality Control
The PVC panels undergo quality control checks to ensure they meet the required standards for durability, color, texture, and other characteristics. Testing may include checking for resistance to moisture, fire, and UV degradation.
6. Packaging
Once the panels pass the quality control tests, they are packaged for shipment. Packaging materials must protect the panels during transportation and storage, and the finished products are packaged in bulk or smaller units depending on customer requirements.
4. Operational Costs
The operational costs of running a PVC Panel Manufacturing Plant include:
- Raw Material Costs: The cost of PVC resin, additives, decorative films, and pigments will be a significant part of the operational budget. Market fluctuations in the prices of petrochemicals and additives can affect costs.
- Energy Costs: The extrusion, lamination, and cutting processes require significant energy consumption, primarily in the form of electricity for heating, molding, and cooling.
- Labor Costs: Skilled labor is required for operating machinery, quality control, maintenance, and packaging. Labor costs will vary depending on the location of the plant and the level of automation.
- Maintenance and Overheads: Regular maintenance of machinery and equipment is crucial for smooth operations. Other overhead costs include administrative expenses, insurance, and utilities.
5. Revenue Projections
Revenue for the PVC Panel Manufacturing Plant will primarily come from the sale of the finished panels to wholesalers, retailers, contractors, and direct consumers. The revenue potential depends on the following factors:
- Production Capacity: The higher the production capacity of the plant, the greater the potential for revenue generation. However, large-scale production also requires a larger initial investment and higher operating costs.
- Pricing Strategy: The price of PVC panels will vary depending on factors such as quality, customization, and market demand. Premium designs and eco-friendly options can command higher prices.
- Market Demand: The growing construction and interior design industries will continue to drive demand for PVC panels. Additionally, demand from emerging markets in Asia and Africa presents significant revenue opportunities.
6. Regulatory Compliance
Compliance with local regulations is crucial for the success of a PVC panel manufacturing plant. Key regulatory requirements include:
- Environmental Regulations: Waste management and emissions control will be important to ensure the plant complies with local environmental laws. PVC production generates waste that must be handled properly.
- Product Safety Standards: The plant must adhere to national and international standards for product safety, particularly if the panels are used in residential and commercial buildings.
- Quality Certifications: Obtaining certifications such as ISO 9001 for quality management systems can help build consumer trust and demonstrate the plant’s commitment to producing high-quality products.
Financial Planning and Cost Analysis
Initial Investment
The initial investment will cover land acquisition, building construction, machinery purchase, raw materials, and regulatory compliance.
Operational Costs
Operational costs include raw material procurement, energy consumption, labor, maintenance, and overheads.
Revenue and Profitability
Revenue will come from selling PVC panels to the construction, interior design, and building industries. The plant can achieve profitability through efficient production and strategic pricing.
Media Contact
Company Name: Claight Corporation
Contact Person: Lewis Fernandas, Corporate Sales Specialist — U.S.A.
Email: [email protected]
Toll Free Number: +1–415–325–5166 | +44–702–402–5790
Address: 30 North Gould Street, Sheridan, WY 82801, USA
Website: www.expertmarketresearch.com
Aus Site: https://www.expertmarketresearch.com.au