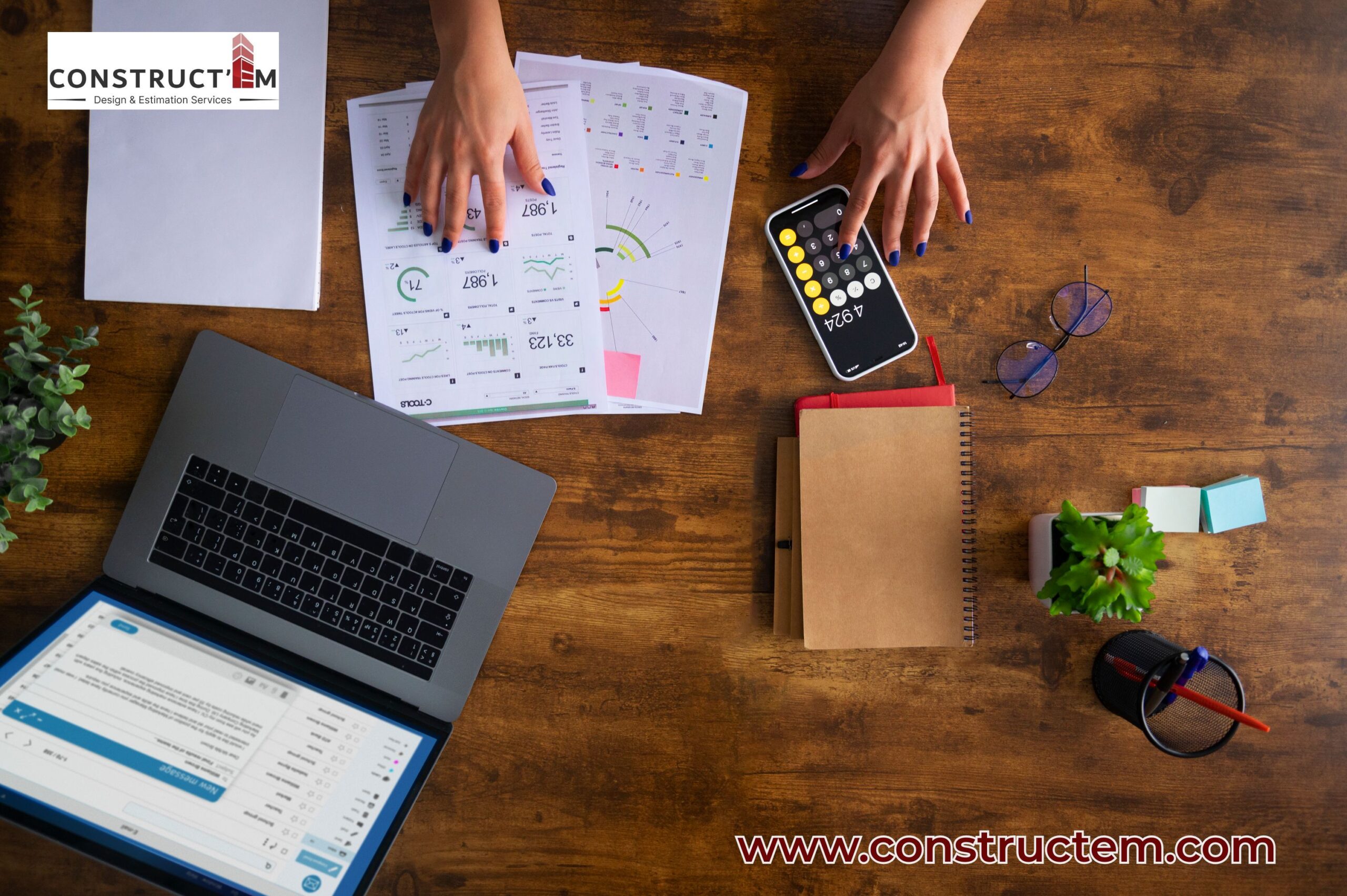
Understanding the Basics of Masonry Estimating
Masonry estimating is a critical process in construction that requires precision and expertise. It involves calculating the costs associated with masonry work, including materials, labor, and other related expenses. Accurate masonry estimates ensure that projects stay within budget and avoid costly overruns.
Key Components of Masonry Estimating
Material Costs
Material costs form the foundation of any masonry estimate. This includes bricks, stones, cement, mortar, and other necessary materials. The type and quantity of materials will vary depending on the project, so it’s essential to assess the needs carefully. Remember to account for waste and potential price fluctuations in your estimate.
Labor Costs
Labor costs are another significant component. These costs depend on the complexity of the project and the skill level of the masons involved. Labor rates can vary by region, so ensure that your estimate reflects local conditions. Additionally, consider the time required to complete the project, as longer projects may increase labor costs.
Equipment and Tool Costs
Masonry projects often require specialized tools and equipment. Estimating the cost of renting or purchasing these tools is essential. Equipment costs can include scaffolding, mixers, and other machinery necessary for the project. Don’t forget to factor in maintenance and transportation costs for these items.
Steps to Create an Accurate Masonry Estimate
1. Site Assessment
Begin by thoroughly assessing the project site. Measure the area where the masonry work will take place and note any potential challenges. These might include uneven terrain, accessibility issues, or existing structures that could affect the work.
2. Material Takeoff
Next, perform a detailed material takeoff. This process involves listing all the materials required for the project and determining the quantities needed. Accurate takeoff is crucial to prevent material shortages or overordering, both of which can impact the project’s budget.
3. Cost Calculation
With your material list in hand, calculate the costs associated with each item. Don’t forget to include taxes, shipping fees, and any other additional costs. For labor, estimate the number of hours required and multiply by the hourly rate. Add equipment and tool costs to the total.
4. Review and Adjust
Once you’ve calculated all costs, review the estimate carefully. Adjust for any potential risks or uncertainties, such as changes in material prices or unforeseen site conditions. It’s wise to include a contingency budget to cover unexpected expenses.
Common Challenges in Masonry Estimating
Dealing with Material Price Fluctuations
One of the biggest challenges in masonry estimating is dealing with material price fluctuations. Prices for bricks, cement, and other materials can vary significantly over time. To mitigate this risk, consider locking in prices with suppliers or including an escalation clause in your contract.
Managing Labor Availability
Another challenge is managing labor availability. Skilled masons are in high demand, and finding qualified workers can be difficult. To address this, plan your project timeline carefully and ensure that you have a reliable labor source before starting the project.
Conclusion
Masonry estimating is a vital skill in the construction industry. Accurate estimates ensure that projects are completed on time and within budget, while also allowing for flexibility in the face of unforeseen challenges. By understanding the key components and following a systematic approach, you can master the art of masonry estimating and contribute to successful construction projects.