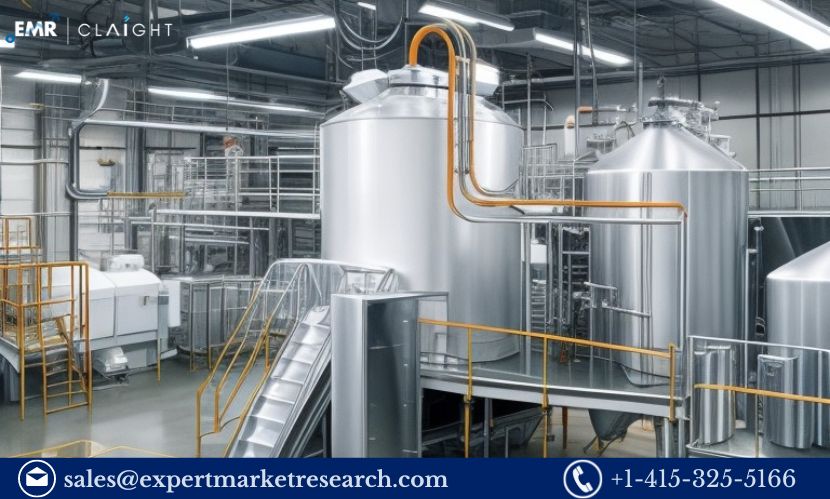
Introduction
Zinc sulfite, a compound primarily used in industrial and agricultural applications, has seen a steady demand due to its versatile uses. From acting as a stabilizer in various processes to being utilized in fertilizers and animal feed, zinc sulfite plays a crucial role in several sectors. The Zinc Sulfite Manufacturing Plant Project Report provides a detailed guide on setting up a facility for producing this compound. This report covers essential aspects such as market analysis, project planning, production processes, and quality control, aimed at ensuring the successful establishment and operation of a zinc sulfite manufacturing plant.
Project Overview
Purpose and Objectives
The main goal of the Zinc Sulfite Manufacturing Plant Project is to establish a facility capable of producing high-quality zinc sulfite efficiently. Key objectives include:
- Efficient Production: Designing a streamlined production process to ensure a steady and reliable output of zinc sulfite.
- Quality Assurance: Implementing stringent quality control measures to produce zinc sulfite that meets industry standards.
- Market Penetration: Capturing a significant share of the zinc sulfite market by optimizing production, distribution, and marketing strategies.
Get a Free Sample Report with Table of Contents @
Market Analysis
A comprehensive market analysis is essential for the success of the manufacturing plant. This analysis includes:
- Demand Assessment: Evaluating the current and projected demand for zinc sulfite across various industries such as agriculture, chemicals, and pharmaceuticals.
- Competitive Landscape: Identifying existing manufacturers, their market share, and competitive strategies to position the new plant effectively.
- Application Trends: Understanding emerging trends in zinc sulfite applications to align production capabilities with market needs.
Project Planning
Site Selection
Choosing the right location for the manufacturing plant is critical. Key factors include:
- Raw Material Access: Proximity to suppliers of key raw materials such as zinc ore and sulfur compounds to ensure a steady and cost-effective supply.
- Infrastructure: Availability of essential infrastructure, including utilities (water, electricity), transportation links, and waste management facilities.
- Regulatory Compliance: Ensuring the site complies with local zoning laws, environmental regulations, and industry standards.
Regulatory Compliance
Compliance with regulations is crucial for operating the plant legally and safely. Key regulatory aspects include:
- Licensing and Permits: Obtaining necessary licenses and permits from local authorities and regulatory bodies.
- Safety Standards: Adhering to safety regulations related to the handling of hazardous materials and ensuring worker safety.
- Environmental Regulations: Complying with environmental regulations regarding emissions, waste management, and overall environmental impact.
Technology and Equipment
The production of zinc sulfite requires specialized technology and equipment. Key components include:
- Reactor Systems: For the chemical reaction that produces zinc sulfite from zinc sources and sulfur compounds.
- Filtration Units: To separate zinc sulfite from other by-products and impurities.
- Drying Equipment: For removing moisture from the final product to ensure stability and quality.
- Packaging Machinery: For packaging zinc sulfite in secure containers for distribution.
Manufacturing Process
Raw Materials
The primary raw materials for producing zinc sulfite are:
- Zinc Ore: A source of zinc used in the production process.
- Sulfur Compounds: Such as sulfur dioxide or sulfuric acid, used to react with zinc to produce zinc sulfite.
Ensuring the quality of these raw materials is essential for maintaining high production standards.
Production Steps
- Preparation: Raw materials, including zinc ore and sulfur compounds, are prepared and measured according to the required formulations for the reaction.
- Reaction: The prepared raw materials are introduced into a reactor system where they undergo a chemical reaction to produce zinc sulfite.
- Filtration: The reaction mixture is processed to separate zinc sulfite from other by-products and impurities using filtration units.
- Drying: Zinc sulfite is dried using specialized equipment to remove any residual moisture and enhance product stability.
- Packaging: The dried zinc sulfite is packaged in suitable containers to ensure it remains stable and uncontaminated during storage and transportation.
- Quality Control: The final product undergoes rigorous testing to ensure it meets quality standards for purity and composition.
Quality Control
Maintaining high-quality standards is essential in zinc sulfite production. The quality control process includes:
- Raw Material Testing: Verifying the quality and suitability of incoming raw materials before use in production.
- In-Process Monitoring: Monitoring production parameters such as reaction conditions, filtration efficiency, and drying processes.
- Final Product Testing: Conducting tests on the finished zinc sulfite to confirm its purity, composition, and compliance with industry standards.
Environmental and Safety Considerations
Environmental Impact
The production of zinc sulfite can have environmental implications. Addressing these impacts involves:
- Waste Management: Implementing systems for the safe disposal and treatment of chemical waste generated during production.
- Emission Control: Using technologies and practices to minimize emissions and comply with environmental regulations.
Safety Measures
Worker safety is a top priority in the manufacturing plant. Key safety measures include:
- Personal Protective Equipment (PPE): Providing appropriate PPE to workers handling raw materials and operating machinery.
- Training: Regularly training employees on safety protocols, proper handling of hazardous materials, and emergency response procedures.
- Safety Equipment: Installing safety features such as emergency showers, eyewash stations, and fire extinguishers.
Financial Analysis
Cost Estimation
Accurate cost estimation is crucial for financial planning. Key cost components include:
- Capital Investment: Costs related to plant construction, equipment purchase, and installation.
- Operational Costs: Ongoing expenses such as raw materials, labor, utilities, and maintenance.
- Marketing and Distribution: Costs associated with promoting and distributing zinc sulfite.
Profitability Analysis
Conducting a profitability analysis helps assess the financial viability of the project. This includes:
- Revenue Forecasting: Estimating potential revenue based on market demand, pricing strategies, and sales channels.
- Return on Investment (ROI): Calculating the ROI to evaluate the financial benefits and sustainability of the project.
FAQ
What is zinc sulfite used for?
Zinc sulfite is used in various applications, including as a stabilizer in chemical processes, a component in fertilizers, and in animal feed. It is valued for its role in enhancing the effectiveness of these products.
What are the main challenges in manufacturing zinc sulfite?
Key challenges include managing the chemical reaction to ensure high yield and purity, handling and storing hazardous materials, and adhering to environmental and safety regulations.
How long does it take to set up a zinc sulfite manufacturing plant?
Setting up a zinc sulfite manufacturing plant typically takes between 12 to 24 months, depending on factors such as site preparation, equipment installation, and regulatory approvals.
What safety measures are required for handling zinc sulfite?
Safety measures include using personal protective equipment (PPE) such as gloves and goggles, providing regular training on safety protocols, and implementing strict procedures for handling and storing hazardous materials.
How can I ensure environmental compliance in the production of zinc sulfite?
Ensuring environmental compliance involves implementing effective waste management systems, controlling emissions, and adhering to local and international environmental regulations. Regular environmental audits and impact assessments can help maintain compliance and minimize environmental impact.
Media Contact:
Company Name: Claight Corporation
Contact Person: Lewis Fernandas, Corporate Sales Specialist — U.S.A.
Email: [email protected]
Toll Free Number: +1–415–325–5166 | +44–702–402–5790
Address: 30 North Gould Street, Sheridan, WY 82801, USA
Website: www.expertmarketresearch.com
Aus Site: https://www.expertmarketresearch.com.au/