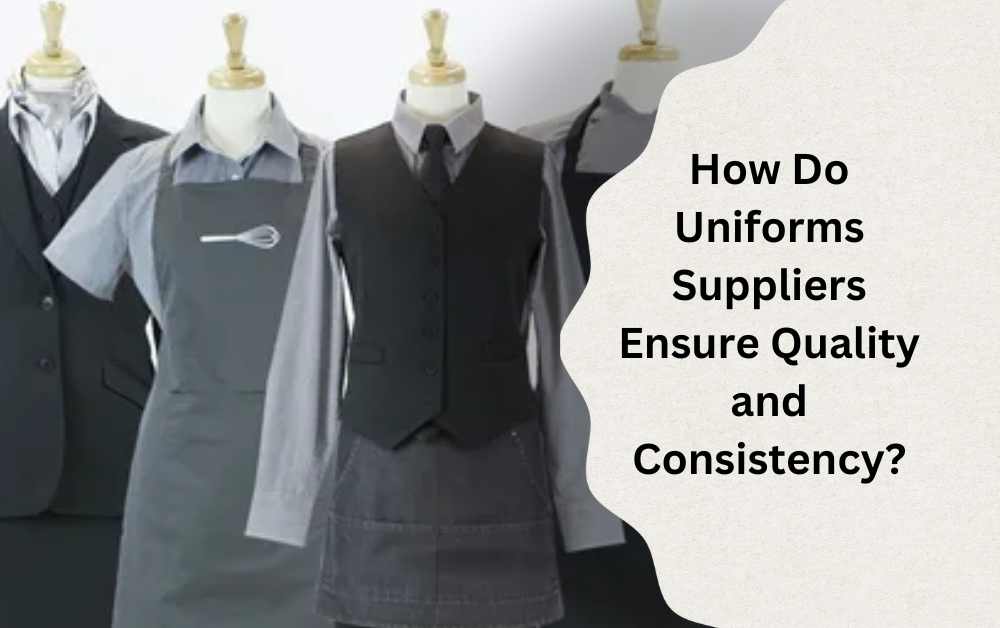
In order to project a professional image, uniforms are essential for organizations in a variety of industries. They serve as a company’s spokesperson to clients and consumers in addition to helping staff feel like a team. Given their significance, uniforms must be of the highest caliber and have a consistent look. We’ll look at how uniform providers maintain consistency and quality while streamlining the process in this blog post.
Understanding the Importance of Quality and Consistency
Why Are Quality and Consistency Important in Uniforms?
High-quality and consistent uniforms are vital for several reasons:
Enhancing Professional Image
Uniforms that are well-made and look consistent across all employees help in creating a positive and professional image for the company. This can build trust and confidence among clients and customers.
Ensuring Employee Comfort
Quality uniforms made from good materials ensure that employees are comfortable throughout their workday. This can lead to increased productivity and job satisfaction.
Promoting Brand Identity
Consistent uniforms with the company’s logo and colors reinforce brand identity and make the company easily recognizable.
Note: Looking for reliable and high-quality uniforms suppliers in Dubai? Trust Al Zarin Uniforms to meet all your uniform needs with unmatched quality and consistency. Our expert team provides comprehensive services from design to delivery, ensuring your business stands out with professional and comfortable uniforms. Contact Al Zarin Uniforms today to elevate your company’s image with the best uniforms in Dubai!
Processes and Practices for Ensuring Quality
What Are the Key Processes for Ensuring Quality?
Uniforms suppliers follow several processes and practices to ensure the quality of the uniforms they produce. Here are some of the key methods:
Rigorous Material Selection
How Do Suppliers Choose the Right Materials?
The first step in ensuring quality uniforms is selecting the right materials. Suppliers choose fabrics that are durable, comfortable, and suitable for the specific needs of the business. For example, uniforms for healthcare workers might require breathable, easy-to-clean fabrics, while those for construction workers need to be rugged and durable.
Suppliers often source materials from reputable vendors and may even conduct quality tests on the fabrics to ensure they meet the required standards.
Advanced Manufacturing Techniques
What Role Do Manufacturing Techniques Play?
Using advanced manufacturing techniques is essential for producing high-quality uniforms. Suppliers employ modern machinery and skilled labor to ensure precision in cutting, sewing, and finishing the garments. Automated machines can handle tasks with high accuracy, reducing the chances of errors and inconsistencies.
Quality Control Checks
How Are Quality Control Checks Conducted?
Quality control is a critical part of the manufacturing process. Suppliers implement stringent quality control measures at various stages of production. This includes:
- Inspecting raw materials: Ensuring the fabrics and other materials meet the required quality standards before production begins.
- In-process checks: Regular inspections during the manufacturing process to identify and rectify any issues immediately.
- Final inspections: A thorough check of the finished uniforms to ensure they meet the company’s specifications and quality standards.
Ensuring Consistency in Uniforms
How Do Suppliers Maintain Consistency?
Maintaining consistency across all uniforms is just as important as ensuring quality. Here are some practices suppliers follow to achieve consistency:
Standardized Production Processes
Why Are Standardized Processes Important?
Standardized production processes ensure that each uniform is made to the same specifications. Suppliers create detailed guidelines and procedures for each step of the production process, from cutting the fabric to adding the final touches. This helps in maintaining uniformity in the finished products.
Detailed Specifications and Guidelines
How Do Specifications and Guidelines Help?
Suppliers work closely with businesses to develop detailed specifications and guidelines for the uniforms. This includes:
- Design specifications: Clear instructions on the design, including colors, logos, and any custom features.
- Measurement guidelines: Standardized measurements to ensure all uniforms fit well.
- Material specifications: Details about the type and quality of materials to be used.
Having these detailed guidelines helps in maintaining consistency across all uniforms.
Use of Technology
How Does Technology Enhance Consistency?
Technology plays a significant role in ensuring consistency in uniforms. Suppliers use computer-aided design (CAD) software to create precise patterns and layouts. This ensures that each piece of fabric is cut accurately, reducing variations in the final product.
Additionally, automated embroidery and printing machines can replicate logos and designs with high precision, ensuring that all uniforms look the same.
Customization and Personalization
How Do Suppliers Handle Customization?
Many businesses require customized uniforms to reflect their brand identity. Uniforms suppliers offer various customization options while still ensuring quality and consistency.
Embroidery and Printing Services
What Are the Benefits of Embroidery and Printing?
Embroidery and printing are common methods of adding logos and other branding elements to uniforms. Suppliers use high-quality embroidery and printing techniques to ensure that the designs are durable and consistent across all uniforms.
Personalized Fittings
How Do Personalized Fittings Ensure a Good Fit?
Suppliers often provide personalized fitting services to ensure that each uniform fits the individual employee well. This can include on-site fittings or detailed measurement guides. Ensuring a good fit not only improves comfort but also maintains a professional appearance.
Ongoing Support and Feedback
How Do Suppliers Support Businesses After Delivery?
Ensuring quality and consistency doesn’t end with the delivery of uniforms. Professional uniforms suppliers offer ongoing support and actively seek feedback from businesses to continuously improve their products and services.
Regular Feedback
Why Is Feedback Important?
Suppliers encourage businesses to provide feedback on the uniforms’ quality and fit. This helps in identifying any issues and making necessary adjustments in future orders.
Reordering and Adjustments
How Do Reordering and Adjustments Work?
Businesses often need to reorder uniforms as they hire new employees or replace old ones. Suppliers keep detailed records of previous orders to ensure that new uniforms match the existing ones in terms of quality and design. They also make adjustments based on feedback to improve the uniforms.
Conclusion
Choosing the right uniforms supplier is essential for ensuring that your business’s uniforms are of high quality and consistent in appearance. Professional uniforms suppliers follow rigorous processes, including material selection, advanced manufacturing techniques, and stringent quality control checks, to produce high-quality uniforms. They also use standardized production processes, detailed specifications, and modern technology to maintain consistency across all uniforms.
For more insightful articles related to this topic, feel free to visit: bigbizstuff.